5 Must-Know Construction Cost Estimates for Project Success
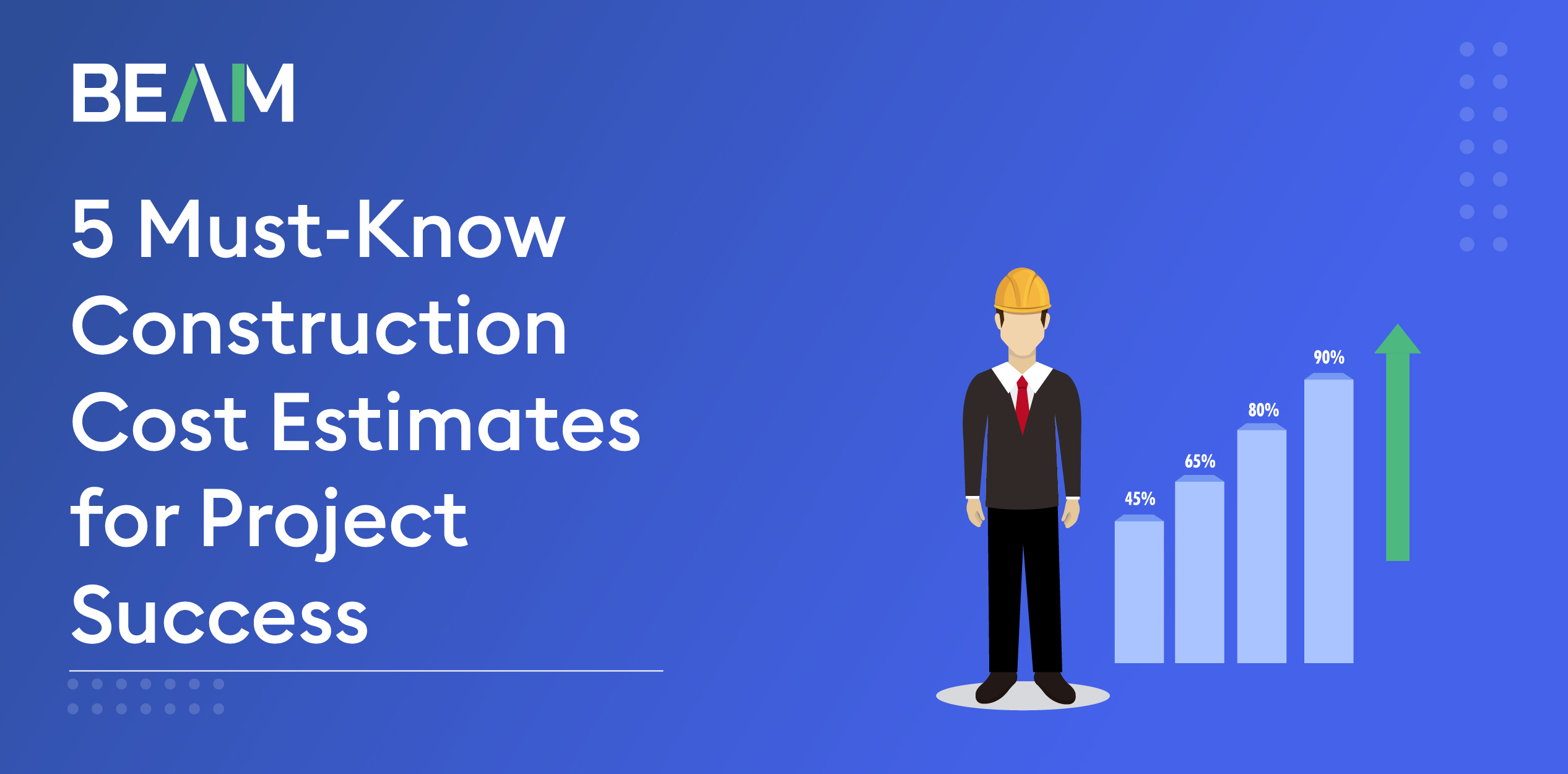
Every construction project starts with one critical step: cost estimation. Get it right, and you’re on track for success. Get it wrong, and you risk blowing your budget, missing deadlines, or disappointing your clients.
Cost estimates aren’t one-size-fits-all. From setting early budgets to controlling costs during construction, each type of estimate has a specific role. And if you’re not using the right one at the right time? You’re setting yourself up for trouble—missed opportunities, overspending, or worse, a failed project.
In this blog, we’ll walk you through the 5 types of construction cost estimates, show you when to use each, and explain how they can keep your project on track from start to finish.
5 Types of Construction Cost Estimate
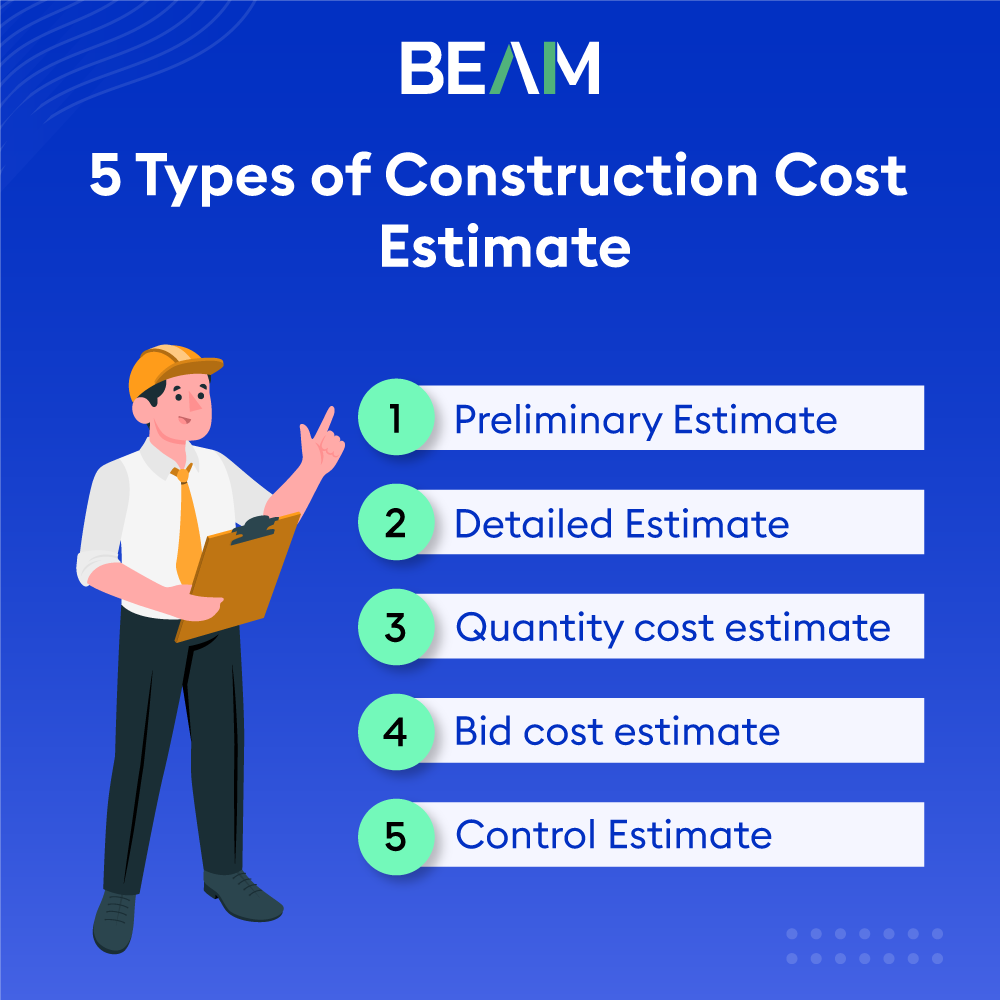
1. Preliminary Estimate
At the start of any project, detailed information is often limited. A Preliminary estimate provides a rough, high-level overview of the potential cost based on the available data. Also referred to as the "abstract cost estimate," it offers clients an initial understanding of whether their project is financially viable.
This estimate considers key factors like land costs, structural components, and trade expenses. General contractors often base it on the costs of similar past projects to offer a realistic starting point.
For example, when planning a new commercial building, a developer might use a cost-per-square-foot approach to see if the project aligns with their budget. Although this method involves a wide margin of error, it’s invaluable for kickstarting meaningful discussions and determining if the project should move forward into more detailed planning.
2. Detailed Estimate
Once the project scope is defined, the next step is to dig into the specifics. A detailed estimate itemizes all costs, including material, equipment and overhead expenses. Think of it as the foundation for accurate budgeting and preparing a detailed estimate requires a final project design.. With construction drawings and specifications in place, estimators can accurately quantify the exact scope of work and calculate associated costs.
For example, when creating a detailed estimate for a commercial office building, a general contractor would calculate precise costs for structural steel, HVAC systems, electrical installations, and interior finishes based on the finalized design documents.
3. Quantity cost estimate
A quantity cost estimate is all about breaking the project into manageable pieces. In this estimate, contractors calculate the materials, labor, and equipment needed for each component, then sum it all up to determine the total cost.
This detailed breakdown is particularly useful for resource planning and procurement. By knowing the exact quantities required, contractors can avoid costly mistakes like overordering or underordering materials.
For instance, consider a retail store construction project. A contractor preparing a quantity cost estimate would calculate the exact amount of concrete needed for the foundation, the square footage of flooring to be installed, and the labor hours required for framing. By quantifying these details early, the estimate ensures efficient resource planning and cost management, ultimately supporting accurate bids and streamlined project execution.
Also Read : Mastering Construction Cost Estimation: Your Ultimate Step-by-Step Guide
4. Bid cost estimate
When preparing a bid, contractors need an estimate that reflects all project expenses. Bid cost estimates are crucial at this stage here. This estimate is essentially the contractor’s proposal, detailing all project costs - direct expenses like materials, labor, as well as overhead, profit margins, and contingencies.
Creating a bid cost estimate involves striking a balance. The estimate must be competitive enough to stand out from other bidders while remaining accurate to ensure the project’s profitability. Contractors often rely on detailed takeoffs, past project data, and market trends to prepare these estimates.
For instance, when bidding on a commercial office building, contractors might break down costs into materials, labor, equipment, overhead, and profit margins. They’ll also account for contingencies to address any unforeseen challenges. The goal is not just to win the project but to ensure that the bid aligns with both the client’s budget and the contractor’s financial budget.
5. Control Estimate
The control estimate serves as a dynamic framework for managing project costs throughout the construction process. Unlike a one-time calculation, this estimate evolves throughout the construction process, comprising three distinct stages:
- Initial Budget Estimate for Financing: The initial estimate is prepared to provide a high-level overview of the project’s requirements and secure funding.
- Budgeted Cost After Contracting: Once contractors are hired and contracts are finalized, the control estimate is refined to reflect agreed-upon terms and pre-construction costs.
- Estimated Cost to Complete (ETC): Cost estimates are updated regularly during construction to track spending and predict remaining costs.
The control estimate is continuously reviewed and adjusted to account for changes such as customer orders, unexpected delays, or market fluctuations.
For instance, in a large-scale infrastructure project like a highway expansion, the control estimate is used to monitor spending on materials such as asphalt and labor costs. If material prices spike due to supply chain disruptions, the control estimate allows project managers to adjust allocations, renegotiate supplier terms, or revise schedules to minimize the impact.
The Bottom Line
Cost estimation lays the foundation for effective pre-construction planning, but it’s not a one-size-fits-all process. Each type of cost estimate carries its own purpose that dictates how the decisions are made at every stage of the project.
Understanding when and how to use each type of estimate ensures that your projects remain financially sound and aligned with client goals. From evaluating initial feasibility to managing costs during construction, a clear understanding of these estimates empowers you to make informed decisions and keep projects running smoothly.
Table of content
.png)
Related posts
Browse all posts
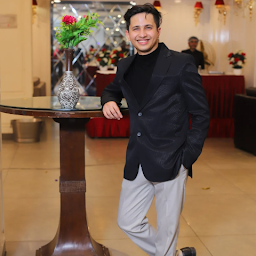
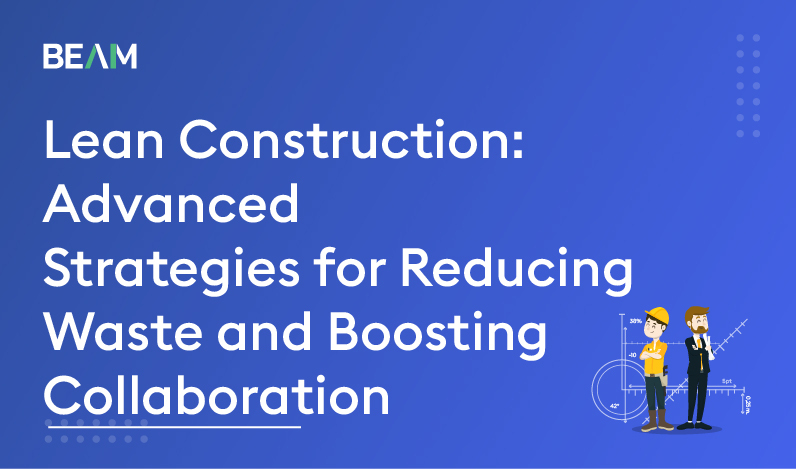
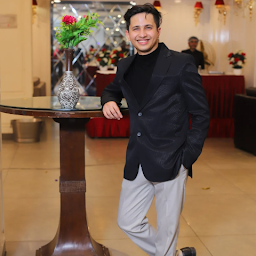
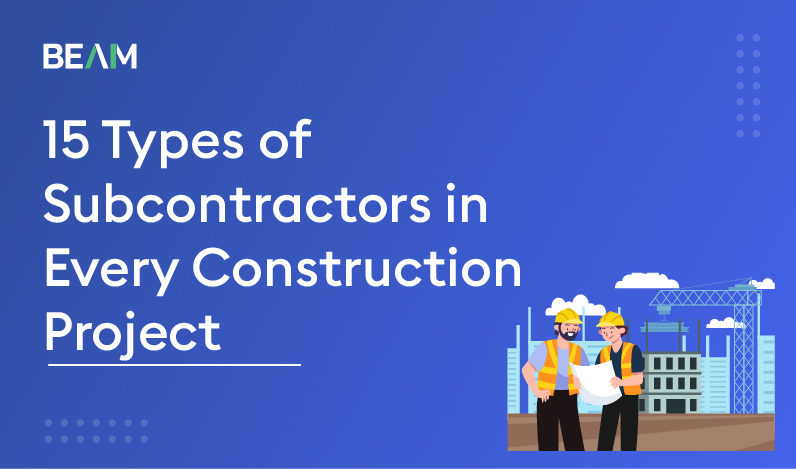
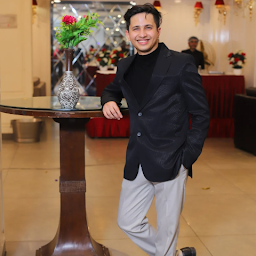