Lean Construction: Advance Strategies for Reducing Waste and Boosting Productivity

Did you know that nearly 80% of large construction projects face delays or cost overruns, according to McKinsey? For many in the construction industry, these issues aren't new - they’re a constant challenge. But there’s a proven approach to cut through inefficiencies and keep projects on track: Lean Construction.
Lean Construction stands out from traditional methods by integrating practical tools like the Last Planner System and Just-In-Time delivery. Unlike traditional approaches that often treat each phase as a separate, isolated process, Lean Construction takes a holistic view. It brings together all team members - contractors, designers, and tradespeople- into a unified planning process.
In this blog, we’ll cover everything you need to know about Lean Construction - from its core principles to practical tools and techniques - so your company can deliver results that set you apart from the competitors.
What is Lean Construction?
Lean Construction is a project management approach that adapts the efficiency-driven principles of the Toyota Production System. It aims to improve the flow of a project by streamlining essential processes in construction. such as material handling, multi-trade coordination, and project scheduling.
At its core, Lean Construction means scrutinizing every step of the process to identify where time, materials, or resources may be wasted. This involves optimizing every process from workflows to coordination between different trades or fine-tuning schedules to avoid delays.
Why Construction Industry Adopting to Lean Construction
The construction industry is adopting lean construction to improve efficiency, quality, and customer satisfaction, while reducing waste and costs. With traditional methods consuming over 40% of the world’s raw resources and contributing an equal share to landfill waste, the need for a streamlined, waste-reducing approach is clear. Lean Construction offers a systematic approach to tackle these issues by creating a more cohesive project environment.
Origins and Evolution of Lean in Construction
Lean Construction principles have their roots in the Toyota Production System (TPS), a manufacturing approach that revolutionized efficiency through practices like Just-In-Time (JIT) delivery and continuous improvement. These concepts, aimed at reducing waste and enhancing quality, have now been adapted for construction. The establishment of the Lean Construction Institute (LCI) in 1997 marked a pivotal moment in helping spread Lean methodologies across the industry.
A notable example of Lean principles in action is the Empire State Building in New York City. This project used Lean techniques to streamline workflows, minimize waste, and improve energy efficiency, ultimately completing the retrofit faster and at a lower cost than traditional methods would have allowed.
5 Core Principles of Lean Construction
Lean Construction centers on a set of core principles that contractors and project managers can apply to keep projects efficient, collaborative, and aligned with client needs. Here’s a closer look at the foundational principles.
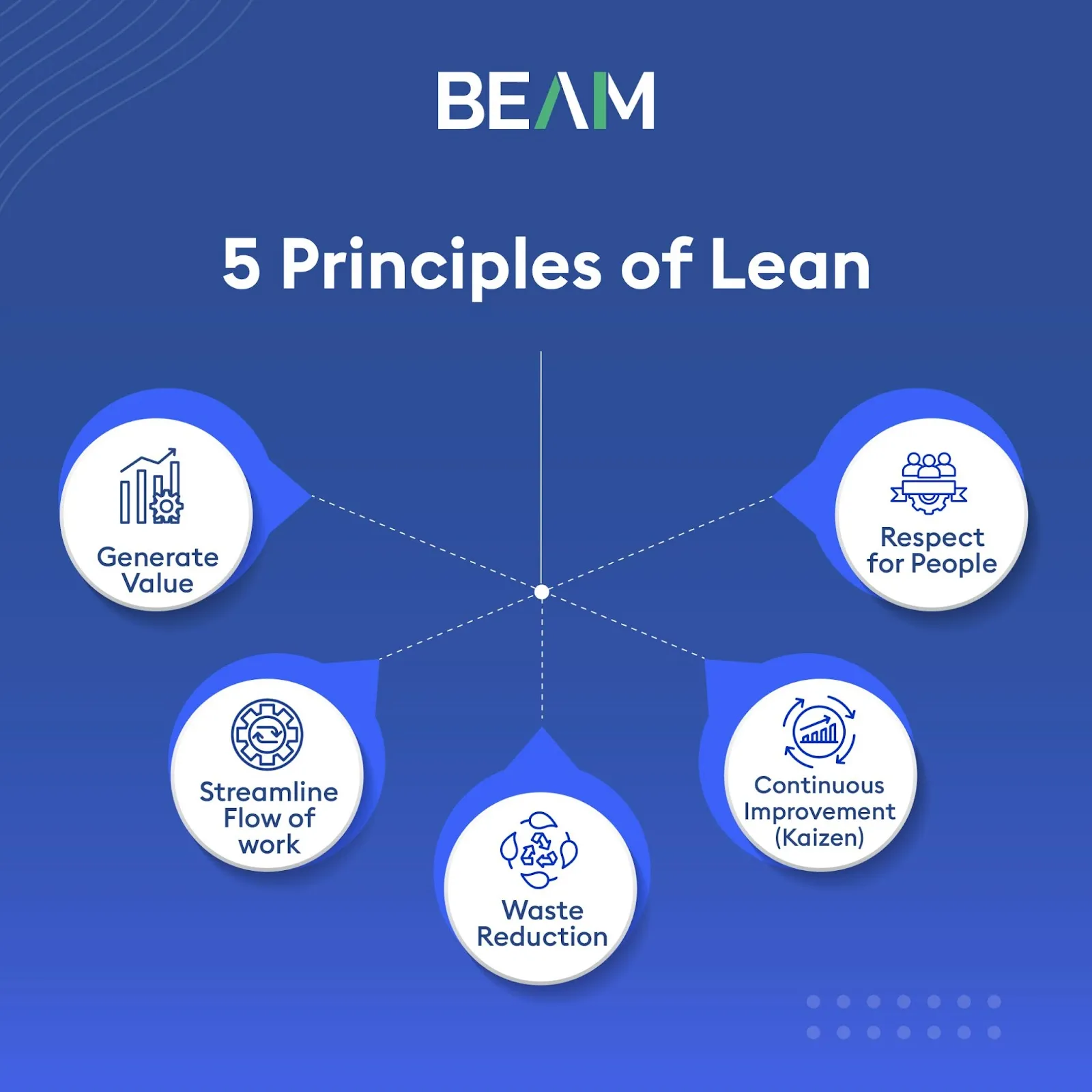
1. Generate Value
In Lean Construction, “value” is defined strictly by the client's needs. Rather than simply delivering what can be done, Lean focuses on understanding the client’s vision and expectations for the project. This principle emphasizes prioritizing what truly matters to the client and allocate time and resources that directly add value. It starts by engaging with clients to understand their expectations, priorities, and long-term vision for the project. It’s only after thoroughly understanding the client’s needs that teams can concentrate resources and efforts on elements that genuinely matter to them.
For instance, in a healthcare facility project, the focus might be on creating efficient care pathways, so every step of the construction should reflect those core needs.
2. Streamline Flow of work
The principle of “Flow” aims to create smooth, uninterrupted work progress throughout the project lifecycle. Construction projects typically involve multiple teams and trades, each one reliant on the completion of prior tasks before they can begin their own. For instance, a flooring team cannot start until the framing team has completed their work. These dependencies often lead to bottlenecks and idle time when tasks aren’t well-coordinated.
Lean Construction addresses these challenges by carefully sequencing and timing work so that every team can move into place exactly when needed.
For example, consider a commercial building project where the electrical, plumbing, and HVAC teams all need to install systems in the same areas. If these teams don’t have clarity on each other’s schedules, they may end up waiting on one another, delaying overall progress.
3. Waste Reduction
Waste is a major issue in construction projects with common forms including surplus materials, unnecessary motion, waiting times, and errors requiring rework. One major reason behind the waste is the misalignment between the design team and trade contractors working on the project. Lean tackles this issue by fostering early collaboration between design teams and trade contractors.
Lean Construction also identifies eight core types of waste - defects, overproduction, waiting, non-utilized talent, transportation, inventory, motion, and over-processing. By addressing these, Lean teams streamline work processes and focus on what truly adds value. For instance, to avoid excess inventory and clutter on-site, Lean teams plan material deliveries to arrive precisely when needed. This “just-in-time” approach prevents storage issues, reduces unnecessary handling, and minimizes the risk of material damage or theft.
4. Continuous Improvement (Kaizen)
Continuous Improvement, or Kaizen, is at the heart of Lean construction. Rather than waiting until the end of a project to assess what could have gone better, Lean Construction encourages teams to make small, ongoing improvements throughout the project. Every team member is encouraged to identify areas for enhancement, no matter how small, and implement changes on an ongoing basis.
For instance, a team might hold weekly “stand-downs” to discuss what worked well, what didn’t, and how they can adjust moving forward.
5. Respect for People
Lean Construction places strong emphasis on collaboration, respect, and valuing each team member’s contribution. Unlike traditional top-down approaches, Lean actively involves all project participants, from executives to laborers, in decision-making and planning. This principle extends to respecting each team member’s skills and expertise and giving them opportunities to contribute effectively in the project. It also involves creating a safe, organized work environment where people feel supported and motivated to do their best work.
The 8 Wastes in Lean Construction
Lean Construction identifies eight core types of waste that disrupt efficiency and inflate costs. These wastes are often summarized by the acronym DOWNTIME:
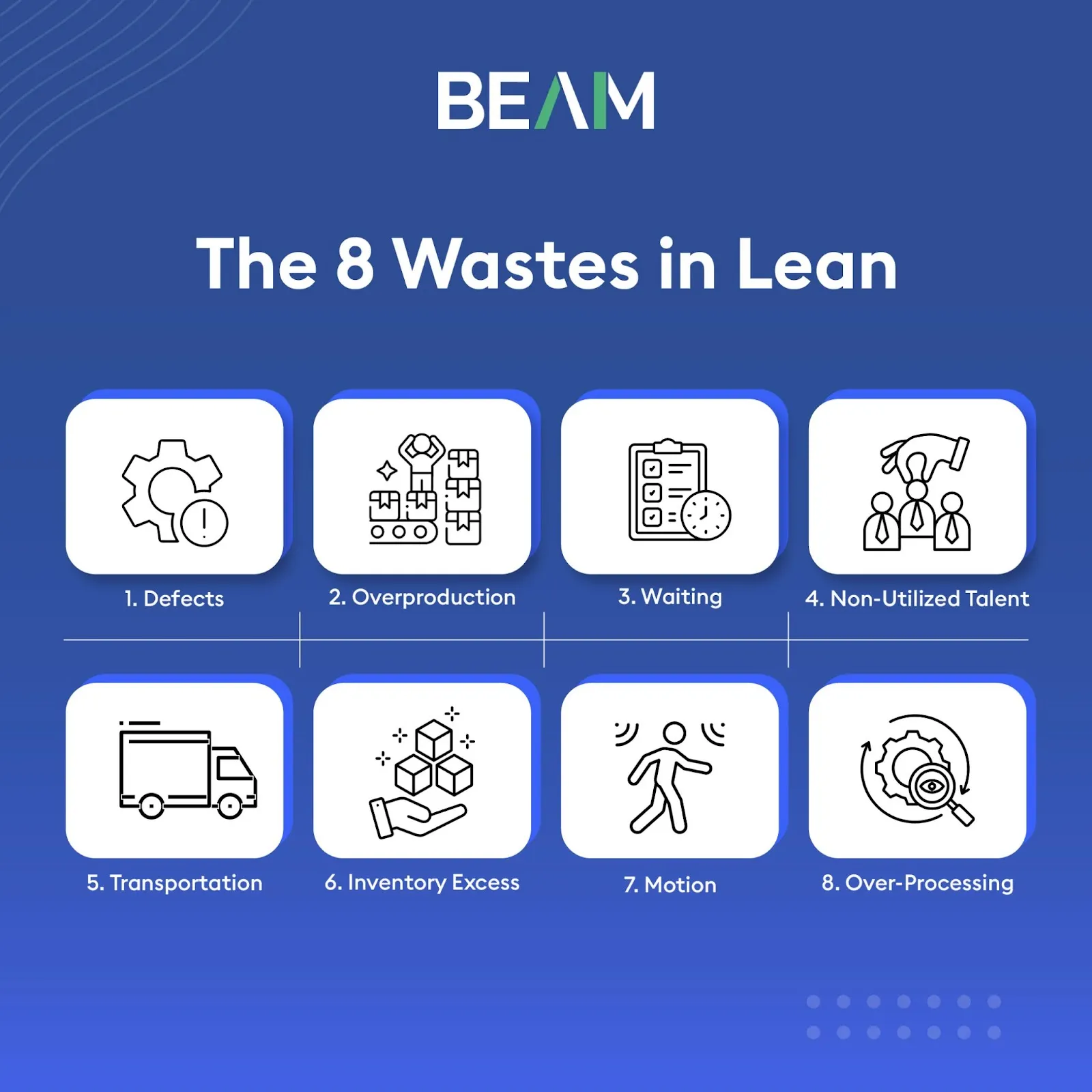
1. Defects
Defects lead to rework, consuming extra time, materials, and labor. For example, an incorrectly poured concrete slab might require a complete redo, affecting the timeline and adding unexpected costs. With rework accounting for nearly 12% of construction costs, Lean practices like early quality checks help tackle these issues early in the process.
2. Overproduction
Overproduction occurs when work is completed before it’s needed. Preparing framing elements too early, for instance, can lead to storage issues and handling costs, particularly if specifications change and the work requires adjustments.
3. Waiting
Waiting is one of the most visible wastes on a construction site which can occur due to multiple reasons such as, delays in material deliveries, awaiting approvals, or dependencies between trades. For instance, a roofing team might wait for the structural framework to be completed or inspected before beginning work, which leads to costly downtime and delayed project delivery.
4. Non-Utilized Talent
When skilled workers are placed in roles that don’t utilize their expertise, valuable potential is wasted. For example, assigning a master electrician to perform basic installation work that could be handled by a junior technician. A survey by the National Association of Landscape Professionals found that underutilization leads to a 15% productivity loss.
5. Transportation
Unnecessary transportation of materials increases labor and equipment costs. For instance, if materials are stored far from the worksite, multiple trips may be required, causing delays and driving up expenses.
6. Inventory Excess
Excess inventory on construction sites can lead to storage issues, increased handling requirements, and even material degradation. For instance, over-ordering bricks or tiles can create clutter on-site, complicating movement and increasing the risk of damage.
7. Motion
Motion waste occurs when workers need to make unnecessary movements to complete tasks. This could include excessive walking between different areas of the site to gather tools or materials. Creating organized workstations and strategically placing tools and materials near work zones helps cut down on wasted motion.
8. Over-Processing
Over-processing involves putting extra effort into tasks that don’t add value to the final product. For example, excessive polishing of surfaces that won’t be visible post-construction consumes valuable time without enhancing quality.
Benefits of Lean Construction
Lean Construction offers a range of practical benefits that address common challenges in the construction industry. Here’s a closer look at the key benefits:
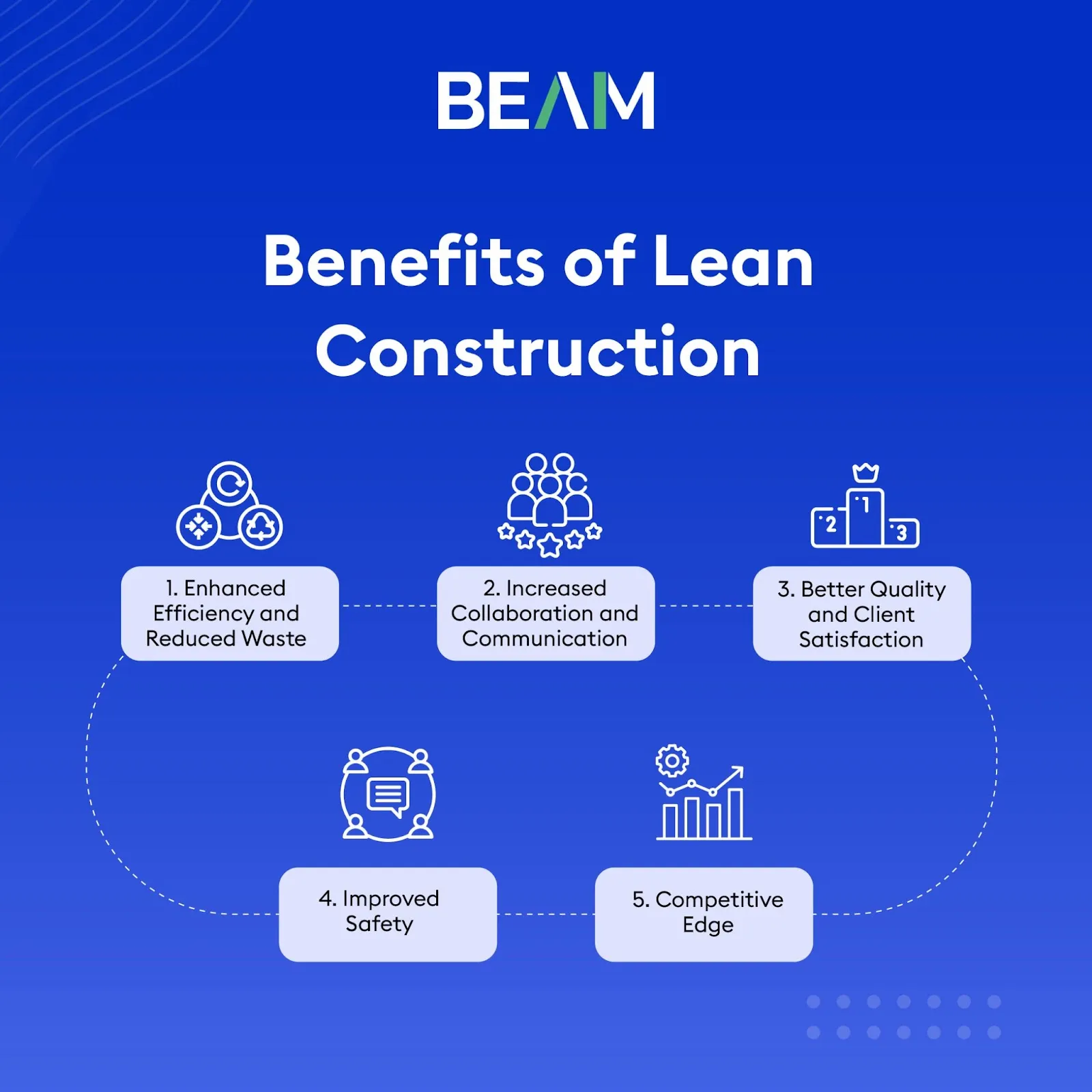
1. Enhanced Efficiency and Reduced Waste
One of the biggest advantages of Lean Construction is its focus on reducing waste while boosting efficiency. Traditional construction often leads to unused materials, idle time between phases, and unexpected rework that can throw projects off track. Lean takes a different approach by carefully aligning resources with project schedules and cutting out non-essential tasks. The result? Contractors can complete work faster and with fewer interruptions, while clients benefit from a more predictable timeline and reduced risk of budget overruns.
2. Increased Collaboration and Communication
Teams often work in silos during the project, with limited communication across various trades and stakeholders. Lean principles help bridge these gaps by promoting a collaborative, transparent environment from day one. With tools like the Last Planner System (LPS), teams come together regularly to review schedules, address challenges proactively, and ensure everyone’s on the same page.
3. Better Quality and Client Satisfaction
Lean construction centers on delivering what the client truly values. By engaging clients in the planning process and continuously refining workflows, Lean Construction aligns project deliverables with the client’s vision and standards.Take, for example, Target Value Delivery (TVD), a Lean method where teams work within set budget constraints to achieve the highest possible value for the client. For clients, this translates into higher satisfaction, as they receive a project that genuinely meets their expectations.
4. Improved Safety
Lean Construction’s organized approach not only improves efficiency but also promotes safety. Techniques like the 5S system (Sort, Set in Order, Shine, Standardize, Sustain) create a clean and organized work environment, reducing the risk of accidents. With clear pathways, well-organized tools, and a clutter-free workspace, job sites become safer for everyone involved. Plus, Lean’s emphasis on continuous improvement means that safety practices are regularly reviewed and adjusted to address potential hazards.
5. Competitive Edge
Lean’s commitment to cost control, waste reduction, and efficient timelines directly impacts the bottom line. Contractors adopting Lean often see higher profit margins, as projects are completed within budget and on schedule, with fewer resources wasted on rework or delays.
In fact, the Dodge Construction Network report found that companies applying Lean principles saw 84% higher quality, 80% greater client satisfaction, and a 77% boost in productivity.
Key Tools and Techniques in Lean Construction
Lean Construction employs a variety of tools and techniques that support its core principles.. Here are some of the essential tools and techniques used in Lean Construction:
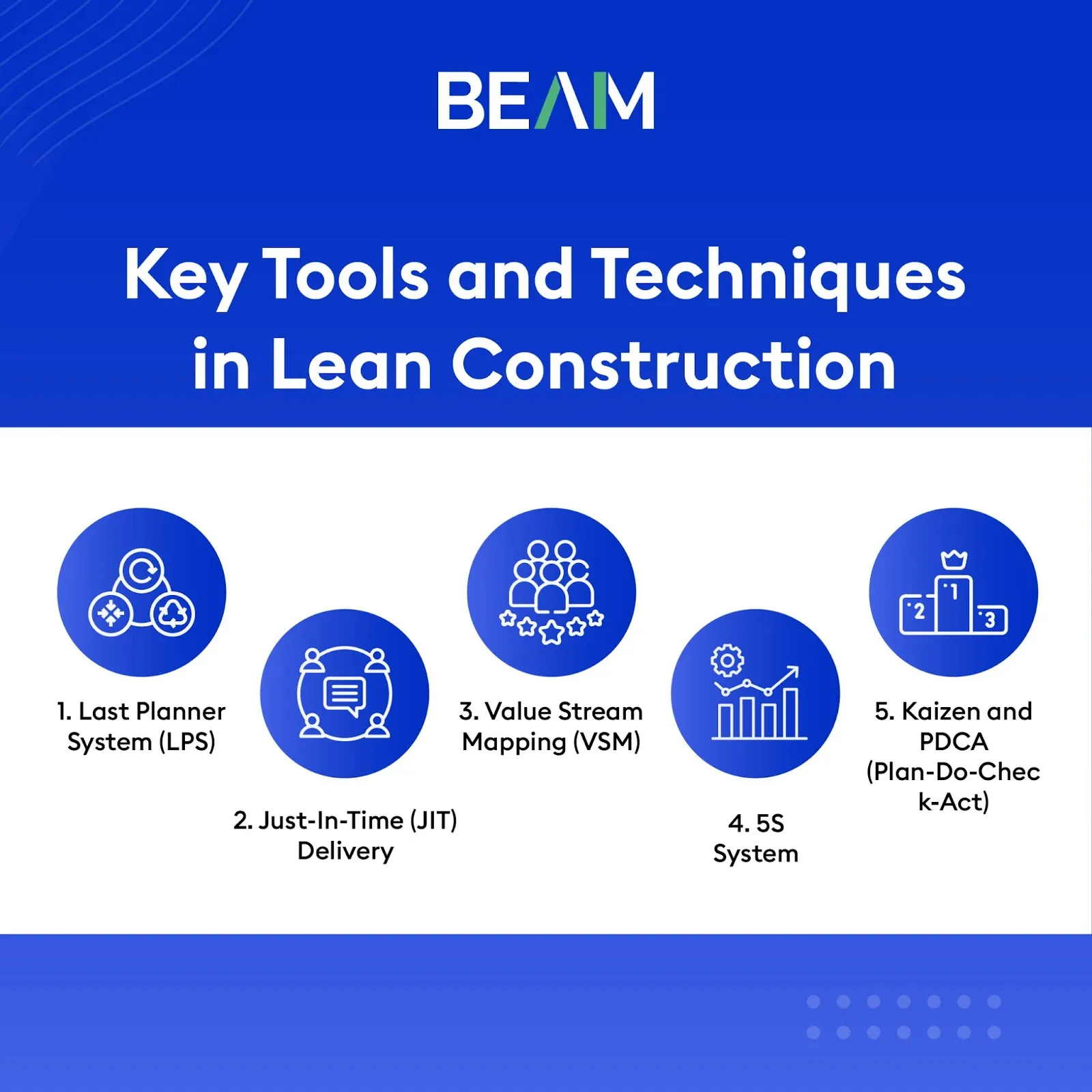
1. Last Planner System (LPS)
Let's talk about the Last Planner System. Think of it as a tool that keeps everyone - from your site managers to subcontractors - on the same page. Instead of a single person dictating timelines, LPS brings the people closest to the work - the “last planners” into the scheduling process.
With LPS, teams break down tasks into manageable, weekly plans, helping everyone stay aligned and keep things running smoothly. As a result, the guesswork is eliminated from the project and each phase of the project progresses smoothly on time.
2. Just-In-Time (JIT) Delivery
Borrowed from Lean manufacturing, Just-In-Time (JIT) delivery minimizes on-site material storage by timing deliveries to arrive only when needed. This approach reduces storage costs, prevents material damage, and improves site organization. With JIT, teams work only with the resources necessary for each phase. This allows for a more organized, efficient workspace and reduces the clutter that can lead to delays or accidents.
3. Value Stream Mapping (VSM)
Value Stream Mapping (VSM) is a visual tool that maps out all steps involved in a construction process, from pre-construction to completion. This mapping allows teams to identify inefficiencies, bottlenecks, and any activities that do not add value to the project. As a result, teams can work together to find opportunities for improvement and align their efforts towards Lean’s goals of maximizing value and reducing waste.
4. 5S System
The 5S system - Sort, Set in Order, Shine, Standardize, Sustain - is an organizational method that keeps job sites clean, orderly, and efficient. Originally developed in manufacturing, 5S helps reduce wasted time by ensuring tools and materials are always in their designated places. This organization minimizes disorganization and chaos on-site, which not only boosts productivity but also promotes a safer, accident-free environment for workers.
5. Kaizen and PDCA (Plan-Do-Check-Act)
Kaizen, meaning “continuous improvement,” and the PDCA (Plan-Do-Check-Act) cycle are fundamental to Lean’s focus on adaptability and continuous improvement. In Lean Construction, these techniques encourage teams to regularly assess their processes, make adjustments, and evaluate the impact of those changes.
With Kaizen, every team member is empowered to suggest improvements. Thereby, creating a proactive culture where problems are addressed before they escalate.
PDCA further supports this by providing a structured framework for testing new approaches, evaluating their effectiveness, and refining them. Together, Kaizen and PDCA create an environment where construction teams continuously improve their methods and outcomes.
How to Get Started with Lean Construction?
Thinking about adopting lean construction but feeling overwhelmed? Here are some actionable tips:
1. Start Small with Pilot Projects
Implementing Lean practices across an entire company or project portfolio can feel overwhelming. Instead, select one or two pilot projects to test Lean techniques. Choose a manageable project size and scope where you can experiment with tools like the Last Planner System or Just-In-Time delivery. This approach allows teams to familiarize themselves with Lean methods, observe what works, and make adjustments before scaling Lean practices company-wide.
2. Invest in Lean Training for All Levels
Lean Construction isn’t just for management; it requires buy-in from every team member. Investing in training for all levels - project managers, field workers, and even clients - ensures that everyone understands Lean principles and practices. Focus on educating your team about core concepts like waste reduction, continuous improvement, and client-defined value. Training should be hands-on and role-specific, so each team member sees how Lean impacts their daily work and feels empowered to contribute.
3. Track and Measure Lean Metrics
To understand the impact of Lean on your projects, it’s essential to track relevant metrics. Choose a few key performance indicators (KPIs) such as cycle time, defect rate, client satisfaction, and cost savings. Regularly analyze these metrics to see how Lean practices are contributing to project outcomes and where improvements can be made. By measuring results, you’ll gain insights into what’s working and what isn’t.
4. Celebrate Small Wins and Recognize Contributions
Lean Construction is an ongoing journey, and progress happens incrementally. Recognize and celebrate small achievements along the way, whether it’s a reduction in waste, a faster task completion, or positive client feedback. Highlighting successes reinforces the value of Lean practices and motivates teams to keep improving. Additionally, recognizing individual contributions fosters a culture of accountability and pride, as each team member sees how their work contributes to the project’s success.
The Bottom Line
If your next project is up against tight budgets and timelines, Lean Construction might be the approach that makes a real difference. Lean Construction represents a paradigm shift from traditional construction approaches, focusing on maximizing value and reducing waste.
Whether you’re managing a large commercial build or a smaller residential project, starting with even a few Lean practices can bring noticeable improvements in efficiency and team alignment. As the construction industry continues to evolve, Lean principles and techniques are proving invaluable for delivering high-quality projects on time and within budget.
Table of content
.webp)