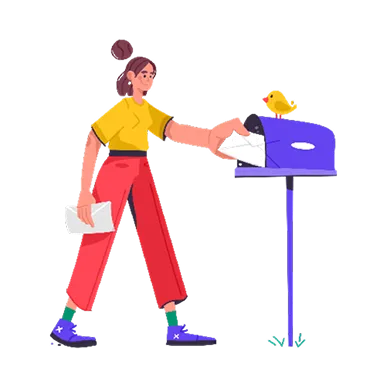
5 Major Construction Risks and How to Tackle Them Successfully
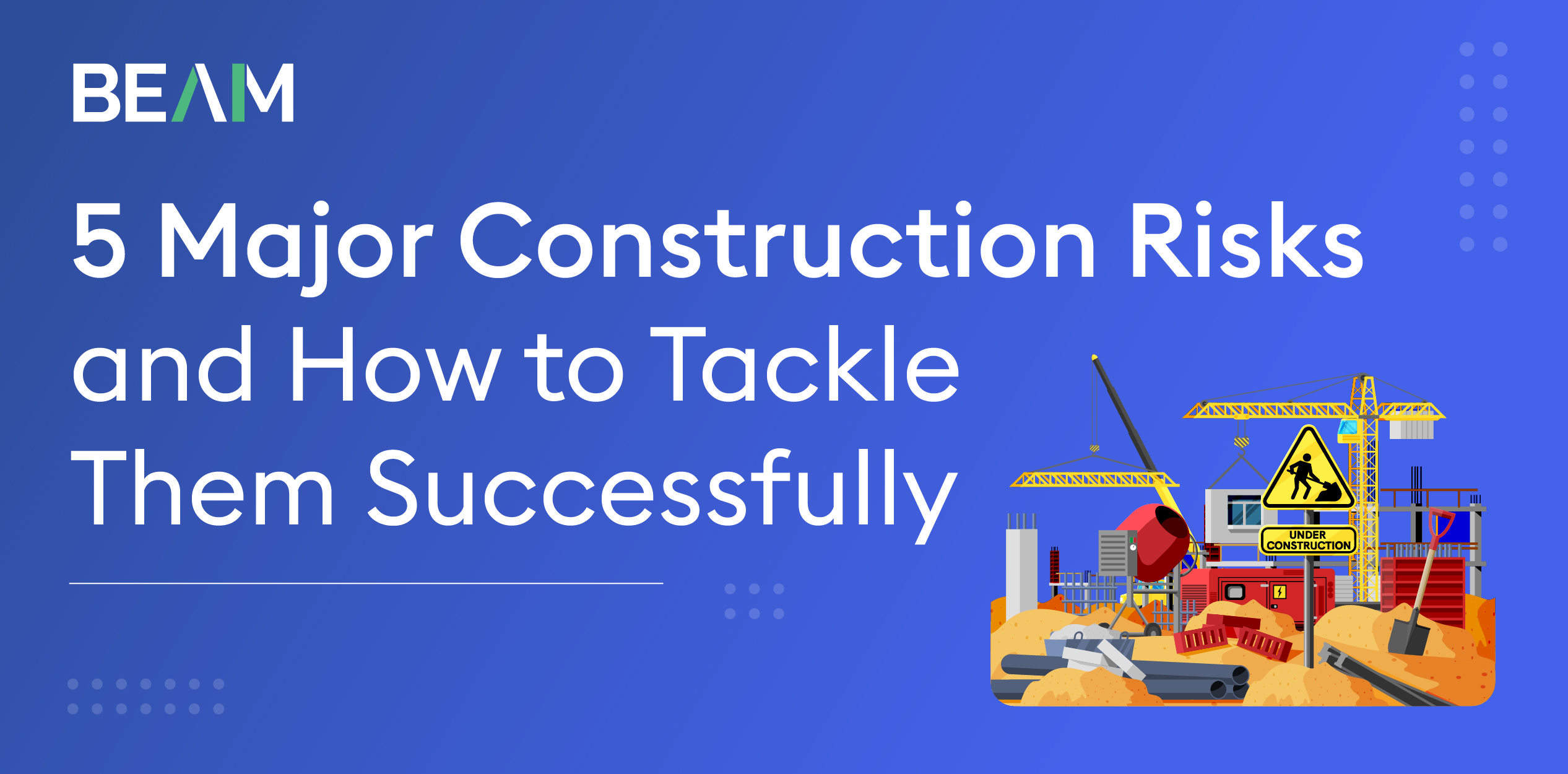
Imagine this: Your team is gearing up for a multimillion dollar construction project. Plans are set, budget approved, and the team is ready to get on field.But then, the unexpected strikes– a labor shortage slows progress, unanticipated site conditions inflate costs, or adverse weather halts operations..
These are the real risks every construction team faces, and they’re more common than you might think. According to a report by McKinsey & Company, over 70% of construction projects exceed their budgets, and nearly 60% face delays, making these challenges all too common.
These risks aren't just bumps in the road–they can derail entire projects. Whether you’re a contractor, subcontractor, or project manager, Knowing how to identify and mitigate these risks is critical to delivering successful projects.
In this blog, we’ll walk through the biggest risks you’re likely to face in construction and, most importantly, how to stay one step ahead. Let’s dive in and simplify risk management for you.
What are Construction Risks?
Construction risks are the potential hurdles that can derail your project’s success–impacting timelines, budgets, and outcomes. These risks are often complex and interconnected, where one issue can set off a chain or problems.
Construction risks generally fall into several categories. Each category presents unique challenges that can hinder project progress. For example, financial risks may involve budget overruns, while operational risks could stem from labor shortages or supply chain disruptions.
By understanding these risks upfront, you can stay proactive and minimize their impact.
5 Biggest Risks in Construction Projects
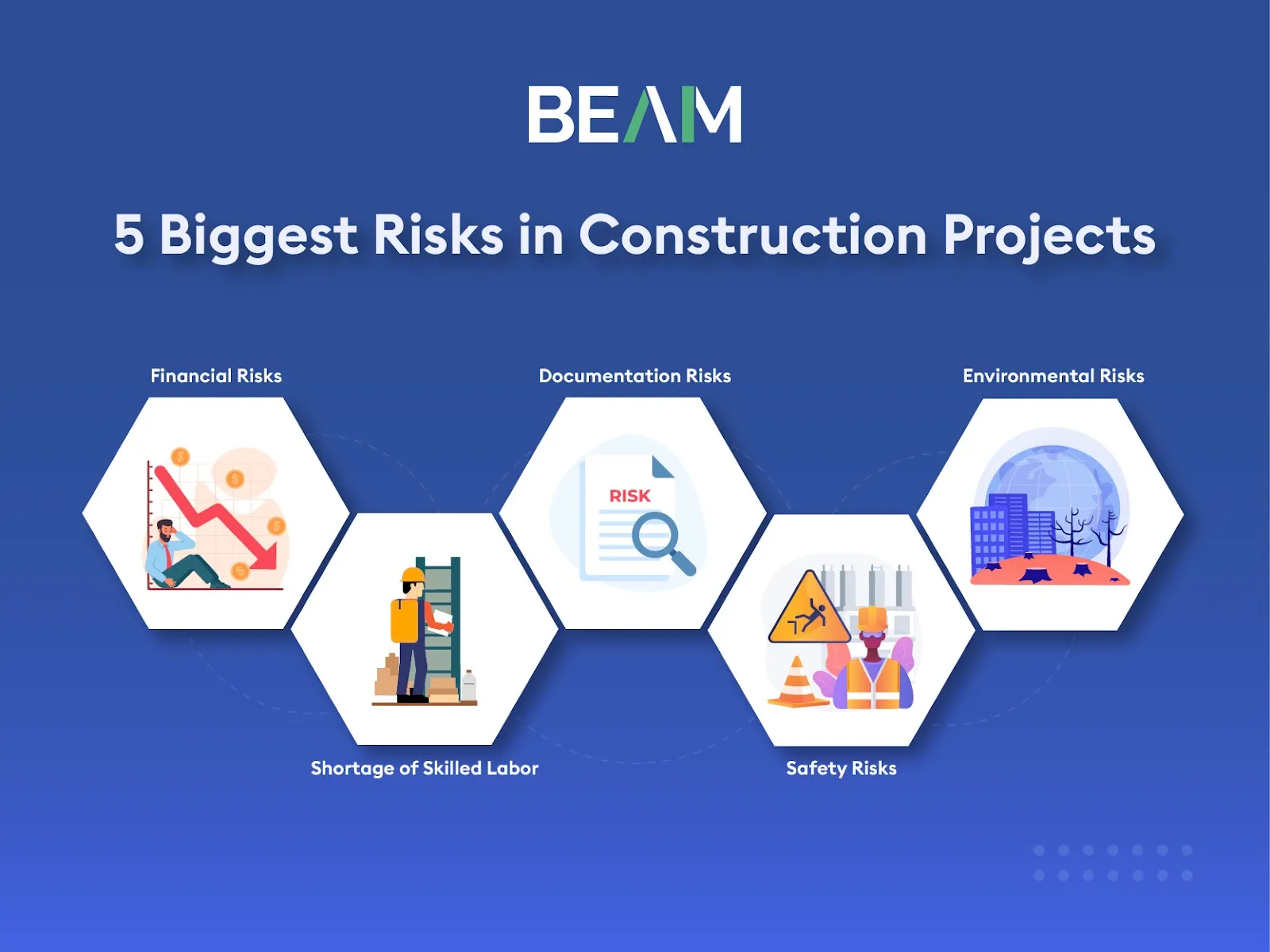
1. Financial Risks
Financial risks are among the most challenging obstacles in the construction industry, encompassing challenges like budget overruns and cash flow gaps. A study by KPMG found that only 31% of construction projects come within 10% of their original budget.
Here’s how these risks manifest:.
- Budget Overruns: Budget overruns occur when actual costs exceed initial estimates, often due to inaccurate takeoffs or unexpected expenses. Takeoffs, the process of determining material quantities for a project, are fundamental in setting a reliable budget. Since they form the basis for the initial estimate and affect the costs of subsequent activities, investing time and effort into detailed takeoffs is crucial for financial control.
- Cash Flow Management: Cash flow refers to the movement of money in and out of a project. With construction projects requiring significant upfront investment, cash flow gaps can lead to delayed payments and stalled progress. This can create cash flow gaps, especially when unexpected expenses arise. As a result, projects often face timeline delays, halted work, and untimely payments to subcontractors and suppliers.
- Economic Conditions: Construction projects are significantly influenced by broader economic trends. Fluctuations in the market, such as rising material costs or changes in labor rates, can affect both project budgets and timelines. During economic downturns, reduced demand for construction services can also make it harder for companies to sustain financial stability.
How to Mitigate Financial Risks
a. Accurate Budgeting and Detailed Takeoffs
Financial risks often stem from the pre-construction phase, where bids are sent out and budgets are approved. To address this, it is pivotal to ensure accuracy from the beginning by investing time in detailed takeoffs.
Ensure the accuracy of your project’s budget by investing in detailed takeoffs. Consider leveraging AI-powered takeoff tools like Beam AI to accurately estimate material costs.
Read more - 6 Must-Know Tips to Master Construction Takeoffs
b. Regular Financial Monitoring
Implement continuous tracking of expenditures against the project budget. Use project management software that offers real-time financial insights, allowing you to spot and address budget variances early on before they escalate into larger issues.
c. Effective Cash Flow Management
Develop a comprehensive cash flow plan that forecasts financial needs and anticipates potential cash flow gaps. Secure financing early in the process and negotiate favorable payment terms to maintain a consistent flow of funds, preventing delays caused by cash shortages.
d. Market Contingency Planning
Prepare for economic fluctuations by maintaining a contingency fund. Regularly assess market conditions and adjust your project’s budget and schedule to account for unexpected changes in material or labor costs, ensuring that your project stays on track despite market volatility.
2. Shortage of Skilled Labor
The construction industry is grappling with a severe labor shortage, especially in skilled trades. This challenge is heightened by demographic changes, with a significant portion of the workforce nearing retirement and fewer younger workers entering the field.
According to the National Center for Construction Education and Research, 41% of the current construction workforce is expected to retire by 2031. This labor crisis is further complicated by competition for workers across various sectors, making it even harder to attract and retain talent.
Several key factors contribute to this ongoing problem:
- Labor Productivity: Labor productivity plays a crucial role in the success of any construction project. However, with fewer skilled workers available, maintaining high productivity levels is becoming increasingly difficult. The lack of experienced laborers can extend project timelines which ultimately results in costly delays and increased expenses.
- Labor Quality: The quality of labor directly impacts the overall success and craftsmanship of a construction project. As the number of skilled workers decline, there are more risks of reduced work quality. This not only affects the project’s schedule and budget but can also damage the reputation of the construction firm involved in the project.
- Labor Availability: The shortage of skilled labor also impacts project scheduling. With a limited workforce, project managers often struggle to allocate enough labor across multiple projects simultaneously. This can lead to delays as projects compete for the same scarce resources. Moreover, the unpredictable availability of labor can cause disruptions, forcing managers to constantly revise timelines and reallocate resources.
How to Tackle Labor Issues
a. Invest in Training and Apprenticeship Programs
Develop a pipeline of skilled workers by investing in training and apprenticeship programs. Collaborate with trade schools and vocational programs to attract new talent and provide hands-on training.
b. Adopt Technology to Enhance Productivity
Utilize advanced construction technologies, such as automation, prefabrication, and project management software, to boost productivity. These innovations can help offset labor shortages by streamlining tasks, increasing efficiency, and reducing the dependence on manual labor.
c. Implement Workforce Retention Strategies
To retain skilled workers, implement comprehensive retention strategies, including offering competitive wages, benefits, and opportunities for career growth. Creating a positive work environment and recognizing employee contributions can further enhance worker satisfaction and stability within the workforce.
d. Outsource Specialized Tasks
In cases where specific expertise is lacking, consider outsourcing specialized tasks to subcontractors or consultants with the necessary skills. This ensures high-quality work is delivered on time, even when internal resources are limited.
3. Documentation Risks
Documentation serves as the foundation for contacts, regulatory compliance, and project execution. Large-scale projects often involve managing hundreds of documents. Any mismanagement in maintaining these documents can lead to serious issues such as, legal disputes, delays, and non-compliance regulations.
Some key risks associated with improper documentation management include:
- Ambiguities and Discrepancies: Confusion or miscommunication in understanding the documents often stem from poorly drafted contracts, vague language, or inconsistent terms. When contracts lack clarity, they become difficult to enforce which results in legal battles and project delays.
- Non-Compliance with Regulations: Construction projects must adhere to a variety of regulations, including building codes, environmental standards, and safety laws. Failure to comply with these regulations can result in fines, legal action, or even project shutdowns. The complexity and variability of regulations across different jurisdictions add to the challenge, making thorough documentation crucial for compliance.
- Delays in Obtaining Permits: Securing the necessary permits is a critical step in construction, but delays in this process can halt progress. These delays can be caused by bureaucratic inefficiencies, incomplete or inaccurate permit applications, or changes in local regulations. Effective documentation helps ensure a smoother permitting process, minimizing the risk of project delays.
How to Mitigate Documentation Risks
a. Draft Clear and Precise Contracts
Work with experienced legal professionals to draft clear, precise contracts that leave no room for ambiguity. Review contracts in detail to ensure that all terms and conditions are well-defined and consistently applied across the project.
b. Ensure Regular Compliance Audits
Conduct a detailed audit every time you take up a new project to ensure all activities comply with relevant regulations, building codes, and environment laws. Consider taking help from compliance experts to navigate complex regulatory issues and legal complications.
c. Efficient Permit Management
Start the permit application process early and ensure that all required documentation is complete and accurate. Establish good relationships with local authorities to expedite the permitting process and address any potential delays promptly.
d. Centralized Documentation Systems
Use centralized digital systems to manage all project documentation. This reduces the risk of miscommunication, ensures easy access to updated documents, and helps maintain consistency across the project.
4. Safety Risks
Safety risks are a major concern in the construction industry, where the nature of the work exposes workers to a variety of hazards. According to the Bureau of Labor Statistics, falls, slips, and trips are the leading causes of fatalities in construction.
Maintaining safety standards in the construction industry is particularly challenging due to the dynamic and evolving nature of construction sites. Each phase of a project introduces new hazards, and even minor lapses in safety procedures can lead to severe accidents.
The Occupational Safety and Health Administration (OSHA) identifies the "Fatal Four" hazards as the most common causes of fatalities in construction:
- Falls: Falls from heights are the leading cause of injuries and fatalities in construction. Whether from scaffolding, ladders, or roofs, falls pose a significant danger if proper safety measures, such as harnesses and guardrails, are not implemented.
- Struck-By Incidents: Workers are at risk of being struck by moving vehicles, falling objects, or machinery. These incidents typically occur in busy, congested areas where visibility and communication are vital for preventing accidents.
- Electrocutions: Working near electrical power sources presents the risk of electrocution. This hazard arises when workers come into contact with live wires, use faulty equipment, or fail to follow safe work practices around electricity.
- Caught-In/Between Accidents: These accidents happen when workers are trapped between heavy machinery, collapsing structures, or materials. They can result in serious injuries or fatalities if safety protocols are not followed closely.
How to Mitigate Safety Risks
a. Organize Safety Training Programs
Establish comprehensive safety training programs tailored to the specific roles and responsibilities of all workers. These programs should include regular refresher courses to reinforce safety protocols and ensure that workers are fully equipped to manage potential hazards on the job.
b. Mandatory Use of Protective Equipment (PPE)
Enforce strict adherence to the use of Personal Protective Equipment (PPE) on-site. Conduct regular inspections of safety gear to ensure compliance with industry standards and provide training on its proper use to reduce the risk of accidents.
c. Frequent Safety Audits
Perform regular safety audits and inspections to proactively identify and address potential hazards. Safety officers should lead these audits, with immediate corrective actions taken to mitigate any risks identified during the inspection process.
d. OSHA Compliance and Hazard Mitigation
Follow OSHA's guidelines to address and reduce the “Fatal Four” hazards. This includes installing guardrails to prevent falls, establishing safety zones in high-risk areas, and ensuring proper lockout/tagout procedures for electrical and machinery safety.
5. Environmental Risks
Environmental risks in construction are complex and can have a significant impact on project timelines, costs, and overall outcomes. These risks arise from various factors, including unpredictable weather, unforeseen site conditions, and evolving environmental regulations. Effectively understanding and mitigating these risks is essential for ensuring smooth, sustainable project execution.
- Adverse Weather Conditions: Weather is one of the most unpredictable factors in construction. Severe weather events such as heavy rain, snow, or extreme temperatures can disrupt construction activities, damage materials, and create unsafe working environments. These delays can extend project timelines and lead to increased costs, making weather a critical risk to manage.
- Unforeseen Site Conditions: Unexpected site conditions, such as unanticipated soil composition or the discovery of hazardous materials, can present significant challenges. These conditions may necessitate redesigns, additional excavation, or remediation efforts, causing delays and inflating project budgets.
- Environmental Regulations and Compliance: The construction industry is increasingly regulated with environmental standards designed to minimize its impact on ecosystems. Compliance requirements range from waste management and pollution control to protecting natural habitats. Non-compliance can lead to hefty fines, legal disputes, and even project shutdowns. As environmental regulations evolve, staying informed and proactive is essential to avoid penalties and ensure projects continue without disruption.
How to Mitigate Environmental Risks
1. Contingency Planning
Incorporate contingencies into your project plan to handle unforeseen challenges. This includes flexible scheduling, safeguarding materials with protective measures, and using weather-resistant construction methods to minimize delays caused by adverse weather conditions.
2. Thorough Site Assessments
Perform comprehensive site assessments before construction begins. Utilize geotechnical surveys, environmental assessments, and utility mapping to identify potential obstacles early, enabling proactive planning and design adjustments that prevent costly delays.
3. Sustainable Construction Practices
Implement sustainable construction practices, such as using eco-friendly materials and minimizing waste, to comply with environmental regulations and reduce the long-term impact of construction activities. This includes integrating energy-efficient designs and technologies that promote sustainability.
4. Regular Environmental Compliance Checks
Stay updated on current environmental regulations and ensure continuous compliance throughout the project. Regular environmental audits and adjustments to practices will help you avoid fines, delays, and reputational harm caused by non-compliance.
The Final Words
Managing risks isn’t just about troubleshooting; it’s about creating a culture or proactive planning and innovation. By embracing risk management tools and strategies, your projects can consistently exceed client expectations.
Ready to future-proof your construction business? Start by exploring AI-powered takeoff software today.