Mastering Construction Cost Estimation: Your Ultimate Step-by-Step Guide
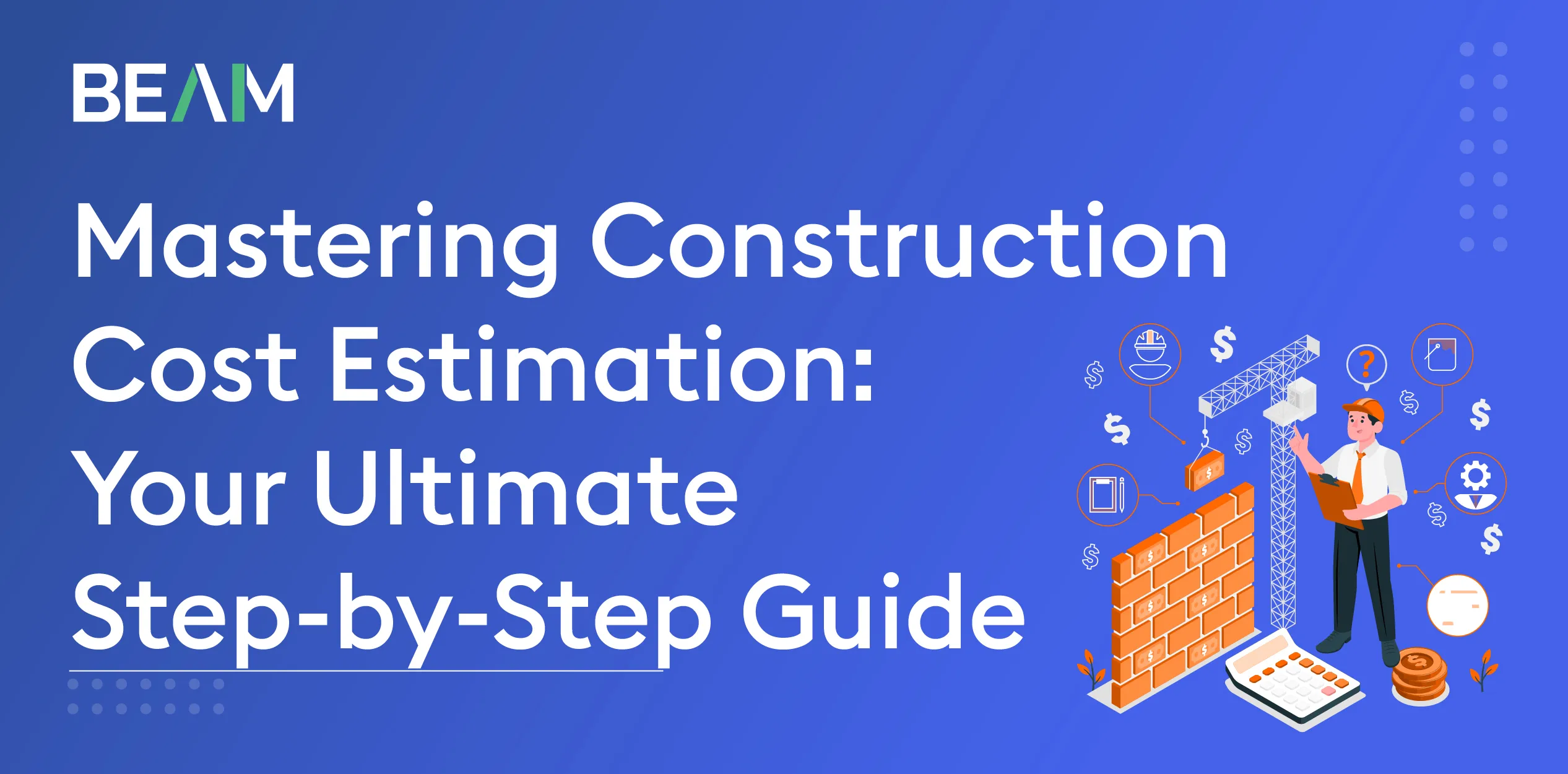
What makes a bid truly stand out? It’s not about who comes in with the lowest estimate for the job—it’s about delivering value, reliability, and trust. Clients today aren’t simply after a number on a page. They want the confidence that their project will be delivered on time, within budget, and to the highest standards of quality. So, how do you go beyond numbers and provide that level of confidence?
The answer lies in creating comprehensive construction cost estimates that set your bid apart from the competition. Accurate estimates help you factor in all costs, foresee contingency costs, plan resources effectively, and protect your margins.
In this guide, we’ll walk you through a step-by-step approach to mastering construction cost estimation. We’ll explore advanced tools, methodologies, and best practices to help you build reliable and precise estimates. Whether you’re aiming to improve your bid quality or streamline your estimating process, these insights will ensure your estimates are accurate, detailed, and ultimately lead to project success.
The Role of Cost Estimating in Project Success
Accurate estimates give project managers the confidence to plan ahead—whether it’s lining up the right crews, securing materials, or avoiding costly overruns. With the right numbers, you make decisions that keep the project moving and profitable.
Let’s take a closer look at how accurate cost estimates can influence key areas of a construction project:
1. Staying on Budget
An accurate estimate sets the financial gameplan, keeping each phase of the project within its defined budget. It helps project managers avoid overspending and maintain control over project costs. With a clear budget in place, teams can track spending and make timely adjustments when needed.
2. Contributes in Strategic Resource Allocation
Cost estimates ensure that the right amount of labor, materials, and equipment is available at the right time. This prevents project delays and costly last-minute purchases.
3. Proactive Risk Mitigation
Construction is a high-risk industry, and unexpected issues are common.
Be it sudden price hikes or site issues you didn’t see coming. But with a sharp cost estimate, you can stay ahead of these risks. For example, if your estimate flags potential delays due to material shortages, you can set aside extra budget now, instead of scrambling later.
Spot a likely price increase in steel? Factor it in from the start and adjust your bid. By planning for what could go wrong, you keep your project steady even when things don’t go as planned.
4. Preparing Winning Bids
For contractors, cost estimating is critical to securing new business. An accurate estimate allows contractors to prepare competitive bids that are both profitable and appealing to clients. Misestimating costs can lead to bids that are too high (losing out to competitors) or too low (cutting into profit margins). A well-calculated bid ensures that contractors maintain profitability while staying within the client’s budget.
Also Read: 7 Bidding Mistakes and How to Avoid Them
Steps to Prepare for an Accurate Cost Estimate
The cost estimating process is a step-by-step approach that ensures all components of a project are accounted for, reducing the risk of budget overruns. Below is a comprehensive guide to the process.
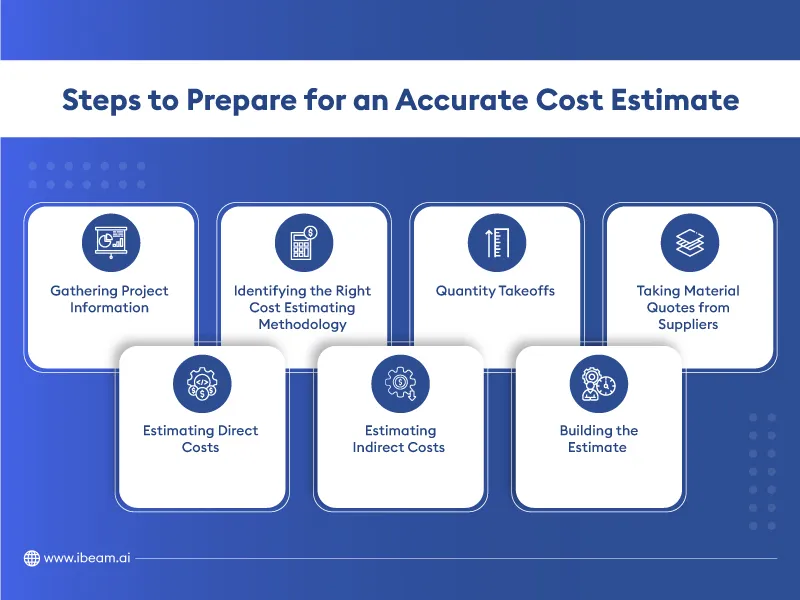
Step 1: Gathering Project Information
Every reliable estimate begins with a solid foundation of project data. The more comprehensive the details, the better equipped you are to make accurate predictions and avoid costly miscalculations. Without this, estimates are prone to errors that can derail an entire project. These are the things to consider while gathering project information:
Project Scope and Requirements:
Every successful estimate starts with a deep understanding of the project's scope.
What are the end goals? What standards and specifications need to be met? Are there specific design elements that require special attention? By documenting these details, you can create a solid plan for the estimating process.
Architectural and Engineering Drawings
The project drawings are the most pivotal aspects of any construction estimate. Detailed drawings provide insights into the project layout, dimensions, and design features, helping you anticipate potential construction challenges.
Bill of Quantities (BOQ)
The Bill of Quantities or detailed project specifications list out everything: the materials, quantities, and quality standards required for the project. These documents act as the benchmark for pricing out materials and labor.
These documents ensure that everyone—from the client to the contractors—is on the same page regarding the project's requirements. The more accurate and detailed this document, the easier it becomes to estimate the true costs of materials and labor.
Site Visit and Assessment
A site visit gives you a real-world perspective on local conditions, identifying any challenges that may impact costs or timelines. Think about the topography—will the terrain make excavation more expensive? What about access points? Will delivering materials require special permits or additional labor? This allows you to factor potential risks into your estimate early on.
Step 2: Identifying the Right Cost Estimating Method
Identifying the right cost estimating methodology is vital because it defines how precise and reliable your estimate will be. The method you choose should align with project details, stage, and required accuracy. These are the various types of cost estimating methods.
Preliminary Estimate
This estimate is typically used in the early stages of project planning when detailed information is scarce. It provides a rough assessment of project costs, helping stakeholders determine the project feasibility without diving into the specifics.
Detailed Estimate
When the project moves into more developed stages, the detailed estimate accounts for all aspects, offering a precise breakdown of labor, materials, and equipment for more accurate budgeting.
Parametric Estimate
The parametric estimating method relies on historical data and statistical models to predict costs based on certain parameters, such as cost per square foot or cost per unit. This method is especially useful when detailed project information is limited but historical data is available.
Unit Cost Estimate
This method provides an accurate breakdown by cost-per-unit, which is especially useful for projects with standardized or repetitive components, like square footage or cubic yards. This method is often used for large-scale projects where consistency in materials and tasks is key.
Step 3: Quantity Takeoffs
Quantity takeoffs make or break your bid. A takeoff provides the total quantities of materials needed for a project. Without a precise understanding of the materials required for a project, it’s nearly impossible to put together a reliable budget.
Overestimate and your bids too high; underestimate, and you risk costly delays from running out of materials. A solid takeoff keeps your bid competitive, your project on track, and waste to a minimum.
Traditionally, estimators use on-screen tools to manually calculate takeoffs by drawing polygons and dragging quantities. However, this process eats up hours—sometimes days—especially on large, complex projects. The time spent on these repetitive tasks leaves little room for strategic tasks like refining estimates.
That’s where AI steps in. Tools like Beam AI are designed to automate the more tedious and error-prone parts of quantity takeoffs, allowing estimators to focus on higher-value tasks. Instead of manually drawing polygons and counting materials, AI-powered software can scan the project drawings and automatically identify areas, materials, and quantities with precision, giving more time to focus on other impactful tasks.
Read more: Takeoff in Construction: The Ultimate Guide
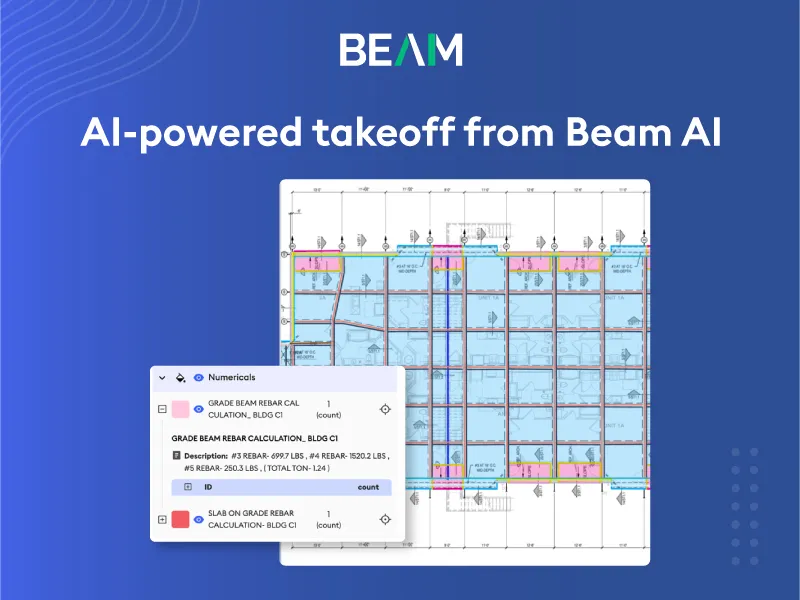
Step 4: Taking Material Quotes from Suppliers
After completing your quantity takeoff, the next step is locking in accurate material pricing. This phase moves you from estimates to real-world costs, ensuring your budget reflects current market conditions. Here’s what you need to do:
Build Supplier Networks for Strategic Advantage
Instead of just gathering quotes, think long-term. Identify suppliers who offer more than just competitive prices. Focus on those who can provide flexibility, faster lead times, or favorable payment terms. When possible, set up agreements for bulk orders across multiple projects to lock in pricing ahead of time, especially in markets where costs fluctuate.
Regularly check in with your suppliers to stay ahead of potential shortages or price hikes, and leverage those relationships for early access to new materials or deals before they hit the open market. Strategic supplier partnerships are just as valuable as cost savings, helping you with leverage when things go sideways.
Evaluate Material Alternatives and Total Lifecycle Costs
Instead of simply balancing price and quality, evaluate material alternatives that offer both short-term savings and long-term performance benefits. For instance, explore recycled or composite materials that may have lower upfront costs or better durability, depending on the project’s needs.
Also, consider materials that reduce installation time or maintenance costs—these can often offset higher initial expenses. Work with suppliers to get samples and run performance tests before making a final decision.
Step 5: Estimating Direct Costs
Direct costs are the expenses that are directly tied to the physical activities on-site. Getting these numbers right is crucial for staying on budget and delivering a successful project. The various direct costs includes:
Labor Costs
Labor costs include everything from hours worked, wages, taxes, insurance, and union dues. On top of that, you have to factor in productivity rates. A skilled crew might charge more, but they’ll get the job done faster. On the other hand, a less experienced team could take longer, pushing up your overall costs.
The goal here is to balance higher hourly rates with faster turnaround times, so you don’t end up overspending on labor.
Material Costs
Materials are another major cost driver in construction, but it’s not as simple as tallying up quantities. You need to account for potential waste, storage needs, and price fluctuations due to market demand.
For example, securing bulk deals early on or negotiating long-term contracts with suppliers can help stabilize costs, especially for larger projects. Keep an eye on market trends, so you’re not caught off guard by sudden price hikes.
Equipment Costs
Equipment costs include expenses for fuel, regular maintenance, and, in some cases, specialized operators. When estimating equipment costs, consider whether renting or buying is more cost-effective for the project’s duration.
For short-term jobs, renting might make more sense, but for long-term projects, buying could save you money. Do the math based on your project’s duration, and don’t forget to factor in downtime and repair costs.
Step 6: Estimating Indirect Costs
Indirect costs aren’t tied directly to the job site but are just as important to keep the project running smoothly. These include:
General and Administrative (G&A) Costs
These cover office overhead, software, utilities, and salaries for your administrative team. Sure, they’re not visible on-site, but without them, project coordination and communication would grind to a halt. Factor these into your estimate—overlooking them could leave you with a budget shortfall.
Project Management Costs
Managing a construction project requires a dedicated team of professionals—project managers, engineers, and schedulers—who oversee everything from timelines to quality control. Their salaries and related expenses must be included in the project budget as indirect costs.
Contingency Funds
Construction projects are inherently unpredictable, and that’s where contingency funds come in. It’s essential to set aside a buffer to cover unexpected expenses—whether it’s price fluctuations in materials, delays due to weather, or unforeseen site conditions. Contingency funds are your safety net, ensuring that unexpected issues don’t derail the project financially.
Step 7: Building and Validating the Estimates
After gathering all the necessary data, the next step is assembling it all into a comprehensive estimate. This is the moment when everything comes together to give you the full financial picture of the project. The goal here is to add up the numbers and ensure that they reflect a realistic view of the project’s costs.
These are the things to consider while building the estimates:
Integrating Direct and Indirect Costs
Start by combining the direct and indirect costs identified in previous steps. Direct costs like labor and materials need to be aligned with indirect expenses, such as administrative overhead and project management costs, to provide a complete overview of the financial requirements.
Make sure you’re not just listing numbers. Ensure they align with the real demands of the project. For example, if you’ve underestimated labor, your indirect costs for project management could balloon as the timeline stretches.
Adding Overhead and Profit Margins
Profit is a key component for any construction project, and it’s important to ensure that a reasonable margin is included in the estimate. Overhead costs, such as general office expenses or company-wide administrative costs, also need to be factored in. These costs might not be specific to one project, but they are necessary to keep the business running smoothly and must be reflected in the estimate.
For instance, if office overhead for your project is expected to spike due to longer communication requirements or extra administrative support, adjust for that. Don’t forget to build in a reasonable profit margin that reflects both the complexity of the project and your company’s long-term goals.
A good rule of thumb: Set a margin that allows flexibility for unexpected snags without undercutting your profitability.
Reviewing and Validating the Estimate
Before finalizing the estimate, it’s essential to review and validate all the data. Cross-check each element—labor rates, material quantities, equipment needs, and indirect costs—to ensure nothing has been missed or miscalculated.
At this stage, you can ask colleagues or stakeholders to review the estimate to ensure accuracy and catch any errors. A well-reviewed estimate reduces the risk of unexpected costs cropping up later, keeping the project on track from both a financial and operational perspective.
Best Practices for Cost Estimation
To further improve the accuracy and efficiency of cost estimates, estimators should follow a set of best practices. These practices help ensure that estimates are both realistic and thorough, reducing the chances of cost estimation mistakes.
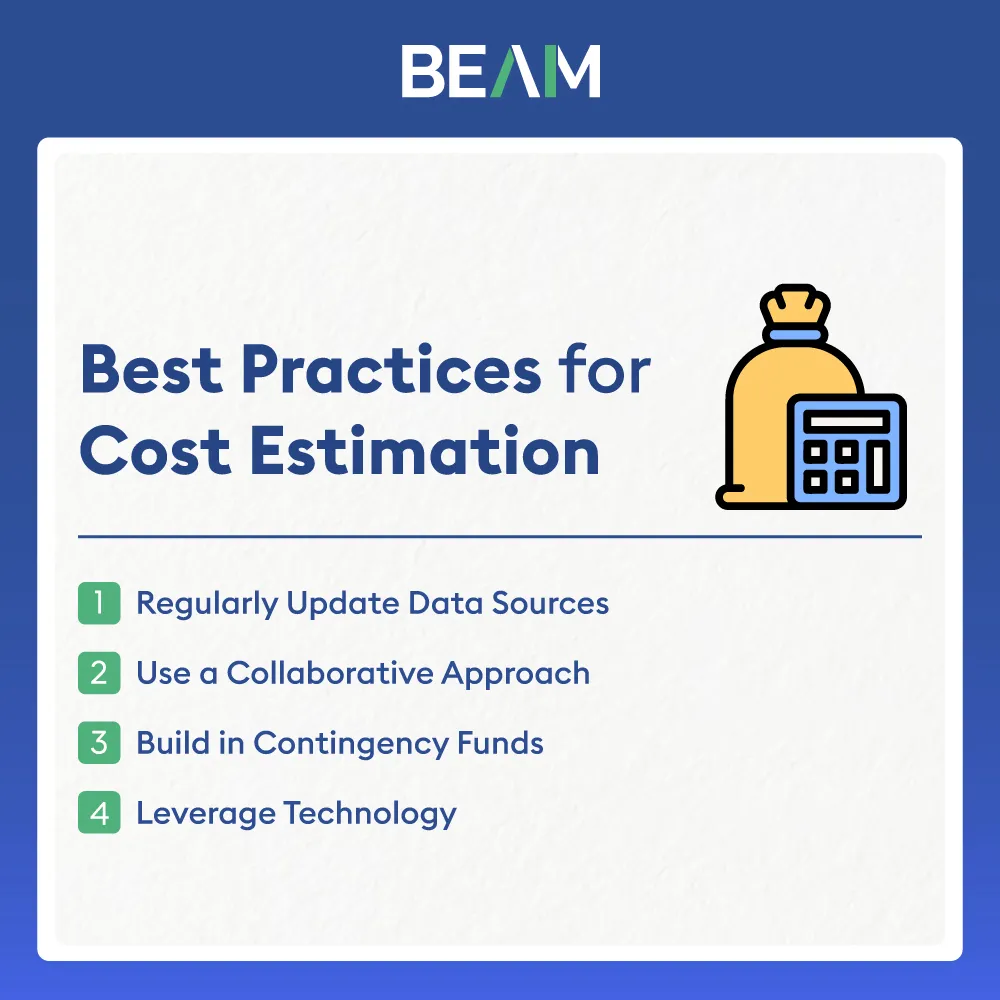
1. Regularly Update Data Sources
Construction costs can fluctuate rapidly due to material shortages, labor market changes, or economic factors. To account for these variables, it’s important to update cost databases and tools frequently, ensuring that estimates are based on the most current information available.
For example, if lumber prices rise unexpectedly, a recent update to your pricing data could save you from underestimating material costs and throwing your budget off-track.
2. Use a Collaborative Approach
Effective cost estimation often involves input from various project stakeholders, including engineers, architects, and suppliers. A collaborative approach ensures that all aspects of the project are considered, and that potential cost risks are identified early.
For example, your engineer might flag a tricky foundation that requires additional materials, or a supplier might warn you about potential delays in getting key materials on-site. By collaborating early on, you’re less likely to be blindsided by unforeseen expenses.
3. Build in Contingency Funds
No matter how detailed or accurate an estimate may be, unforeseen circumstances can arise. Always include contingency funds to cover unexpected expenses. This provides a safety net and prevents budget overruns.
Whether it’s a delay caused by bad weather or a sudden price increase for steel, building in a contingency fund (typically 5-10% of the total project cost) provides a financial buffer. For instance, if a supplier increases their rates midway through the project, that contingency fund can absorb the hit without blowing your entire budget.
4. Leverage Technology
Embrace automation tools to speed up repetitive tasks, such as material takeoffs. Software like Beam AI can automate the more time-consuming aspects of cost estimation, like takeoff, allowing estimators to focus on higher-level decision-making, risk assessment, and fine-tuning the budget.
Tools and Resources for Optimizing Construction Estimates
Accurate construction cost estimates depend on the use of reliable tools and data. As technology evolves, estimators can leverage AI tools to transforming construction estimation process. Let’s take a look at some of the essential tools and data sources that can elevate your estimating process and help you secure more winning bids:
1. Fully Automated AI Takeoff Software
Modern tools like Beam AI have redefined the way estimators work by automating repetitive tasks and streamlining the entire takeoff process.
With features like automated quantity takeoffs and integration with estimating software, Beam AI enables estimators to focus on refining cost estimates and optimizing project strategies rather than spending hours on takeoffs. This automation ensures not only accuracy but also a smoother workflow from start to finish.
2. Historical Data and Industry Benchmarks
One of the most valuable resources in estimating is historical data. By looking at past projects, estimators can make more informed assumptions and better predict the costs of similar future projects. Historical cost data helps refine estimates by providing insights into labor productivity, material usage, and cost fluctuations over time.
Industry benchmarks also offer valuable insights. Comparing a project's expected costs against industry standards ensures that estimates are realistic and competitive. These benchmarks serve as a reference point to validate assumptions and avoid over- or underestimating project costs.
3. Industry Databases for Real-Time Pricing
To maintain accuracy, especially in today’s fast-moving market, access to real-time pricing is essential. Industry databases provide up-to-date information on material, labor, and equipment costs, adjusted for regional pricing differences. These databases are invaluable for ensuring that estimates reflect current market conditions and pricing trends.
By integrating data from reliable sources, estimators can adjust their estimates as market conditions change, minimizing the risk of cost overruns due to outdated pricing information.
Final Words
Accurate cost estimation lays the foundation for any successful construction project. From initial planning to the final bid submission, every stage in the estimating process plays a pivotal role in ensuring projects stay within budget. But for estimators, juggling between these critical activities can be daunting—overemphasizing one aspect often means missing crucial details elsewhere.
This is where technology steps in as a game-changer. Solutions like Beam AI make it easier to tackle the quantity takeoff, providing a solid foundation for creating estimates that are both detailed and accurate. Embracing these innovations ensures that no part of the estimation process is overlooked, allowing you to stay competitive and deliver projects that exceed expectations.
FAQs
1. What is the difference between direct and indirect costs?
Direct costs are expenses that are directly tied to project activities, such as labor, material, and equipment. Indirect costs, on the other hand, includes overhead costs, and contingency funds, which are necessary for the project’s success but not tied to specific tasks.
2. How do takeoffs impact the cost estimation process?
Takeoffs are essential to the cost estimation process as they determine the quantity of materials needed for the project. Accurate takeoffs ensure that material costs, labor, and equipment estimates are reliable, directly influencing the project’s budget and timeline.
Inaccurate takeoffs can lead to over-ordering or under-ordering materials, which causes budget overruns or delays. They also affect the competitiveness of bids, as well-calculated takeoffs allow contractors to submit competitive and profitable bids. Ultimately, takeoffs provide the foundation for accurate cost estimates and effective budget control throughout the project.
3. How do you account for unforeseen costs in a construction estimate?
A contingency fund is usually included to cover unforeseen costs such as price fluctuations, design changes, or unexpected site conditions. The size of the contingency is based on the project's complexity and risk factors.
4. What is the role of technology in improving cost estimation efficiency?
Technology plays a critical role in improving the efficiency and accuracy of the cost estimation process. Advanced tools and software automate time-consuming tasks, such as takeoffs and data calculations, which significantly reduce the risk of human error.
Additionally, technology provides access to real-time data through industry databases, allowing estimators to retrieve up-to-date pricing for materials, labor, and equipment. Furthermore, estimating software also enables better project management through integration with scheduling and resource planning tools, streamlining workflows, and improving collaboration across teams.
Table of content
.webp)