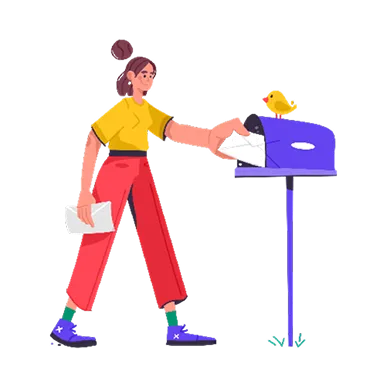
Mastering Cost Control: Strategies to Reduce Operating Expenses in Construction
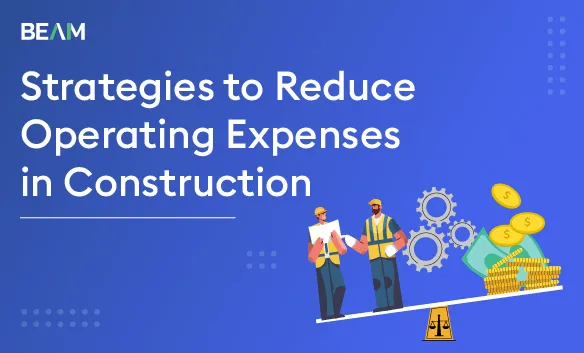
The construction industry is a complex ecosystem where margins are tight and competition is fierce. Every dollar saved is a dollar earned. Amidst rising material costs, labor shortages, and economic uncertainties, controlling operational expenses is paramount for long-term success.
Operating costs are critical in the construction industry, impacting profitability and project success. These costs, encompassing everything from labor and materials to equipment maintenance and unforeseen delays, can quickly escalate if not carefully managed. High operating costs can erode profit margins, hinder competitive bidding, and even jeopardize the long-term sustainability of your business. With the complexity of modern construction projects and the pressures to meet tight deadlines and budgets, controlling these expenses has never been more crucial.
Effective operating cost management requires a deep understanding of both fixed and variable expenses and a proactive approach to cost control. This involves evaluating current expenditures and implementing strategies to minimize waste and maximize efficiency. This guide will delve into practical methods for reducing operating costs.
Understanding Operating Costs in Construction
Operating costs are expenses incurred during a construction business's operation. They can be broadly categorized into fixed and variable costs, including rent, wages, utilities, administration expenses, maintenance, and repairs. Managing these costs effectively is crucial for a construction company's profitability and sustainability.
Strategies for Reducing Operational Costs

Implement Life Cycle Costing
One of the most effective ways to reduce operating costs is to incorporate Life Cycle Costing (LCC) during the planning phase. LCC assesses the total cost of ownership, considering both initial and ongoing costs over the asset's lifespan. This approach allows you to compare different design alternatives and choose the most cost-effective solution.
For instance, when planning a new building, you can use LCC to evaluate various materials and construction methods. By considering factors such as maintenance, energy consumption, and future repairs, you can make informed decisions that reduce long-term costs. This holistic view ensures that you are not just looking at the upfront expenses but also considering the impact on your budget over the building's entire lifecycle.
Key components of LCC:
- Initial costs: Design, permits, construction, and equipment purchase.
- Operational costs: Energy consumption, maintenance, repairs, and staffing.
- Disposal costs: Demolition, waste management, and site restoration.
By carefully evaluating these costs, you can identify opportunities to reduce expenses and improve the overall value of your project.
Embrace Technology
The construction industry is rapidly evolving, with technological innovations playing a pivotal role in reducing operating costs. One significant advancement is using AI-powered takeoff software, like Beam AI. This technology automates quantifying accurate materials from digital plans, significantly reducing the time and effort required for manual takeoffs.
By integrating AI-powered takeoff software, you can streamline your pre-construction phase, minimize human error, and improve overall productivity. This not only lowers your operating costs but also allows you to bid more competitively and win more projects.
Additionally, technologies such as drones, LIDAR, and digital twins provide real-time data and insights, enabling better decision-making and reducing the likelihood of costly rework. These tools allow for more precise planning and monitoring, ensuring that projects stay on schedule and within budget.
Adopt Lean Construction Practices
Lean construction is a methodology that focuses on minimizing waste and maximizing value throughout the construction process. By adopting lean principles, you can improve efficiency, reduce costs, and deliver higher-quality projects.
Key lean construction principles include:
- Identifying Value: Determine what adds value to the project from the client's perspective and focus efforts on those activities.
- Mapping the Value Stream: Analyze the entire construction process to identify and eliminate waste.
- Creating Flow: Ensure that value-creating steps proceed without interruptions.
- Establishing Pull: Produce only what is needed when it is needed, reducing inventory and overproduction.
- Pursuing Perfection: Continuously seek ways to improve processes and eliminate waste.
Implementing lean construction practices can lead to significant cost savings. For example, optimizing scheduling and resource allocation can reduce downtime and avoid costly delays. Lean construction also promotes a culture of continuous improvement, where teams are encouraged to collaborate and innovate, further enhancing efficiency and reducing costs.
Enhance Maintenance Strategies
Effective maintenance strategies are essential for keeping operating costs under control. Regular maintenance ensures that buildings and equipment remain in good working condition, reducing the risk of unexpected breakdowns and costly repairs. There are several maintenance strategies to consider:
- Preventive Maintenance: Scheduled maintenance activities aimed at preventing equipment failure.
- Predictive Maintenance: Using data and analytics to predict when equipment will fail and perform maintenance accordingly.
- Reliability-Centered Maintenance: A comprehensive approach that considers the impact of equipment failure on overall operations and prioritizes maintenance activities accordingly.
By choosing the right maintenance strategy and adhering to a well-defined maintenance plan, you can extend the lifespan of your assets and avoid the high costs associated with unplanned downtime and repairs.
Plan for Environmental Delays
Weather conditions can significantly impact construction schedules and budgets. Extreme temperatures, heavy rain, and high winds can cause delays and increase operating costs. To mitigate these risks, planning for environmental delays in your project estimates is essential. By understanding the weather patterns and site conditions for your project location, you can develop contingency plans and adjust schedules accordingly. For example, scheduling intensive outdoor tasks during cooler parts of the day or using modular construction to avoid weather-related delays can help keep your project on track and within budget.
Optimize Material Procurement
Material procurement and asset tracking are key areas where construction companies can significantly cut operating costs. Efficient procurement involves more than just securing the best prices; it's about strategic sourcing and making informed decisions. Similarly, effective asset tracking prevents costly losses and inefficiencies. Implement technology solutions like Beam AI's AI-powered takeoff software to streamline your inventory management. Integrating automated takeoff software with real-time tracking allows you to monitor materials and tools, manage inventory levels, and set alerts for low quantities. This reduces the risk of misplaced assets, optimizes resource allocation, and reduces costs.
Final Words
Reducing operating costs requires a proactive and comprehensive approach. By integrating strategies such as life cycle costing, embracing technological advancements, and optimizing procurement and asset management, you can achieve significant savings and improve your project outcomes. It's not just about cutting costs but also about making informed decisions that enhance efficiency and value.
As you implement these strategies, consider how technology like AI-powered takeoff software can further streamline your processes and reduce manual effort. By staying ahead of industry trends and leveraging innovative solutions, you position your business for long-term success and resilience in a competitive market. Start applying these cost-saving strategies today and experience the difference in operational efficiency.