The Future of Construction: Trends to Watch in 2025
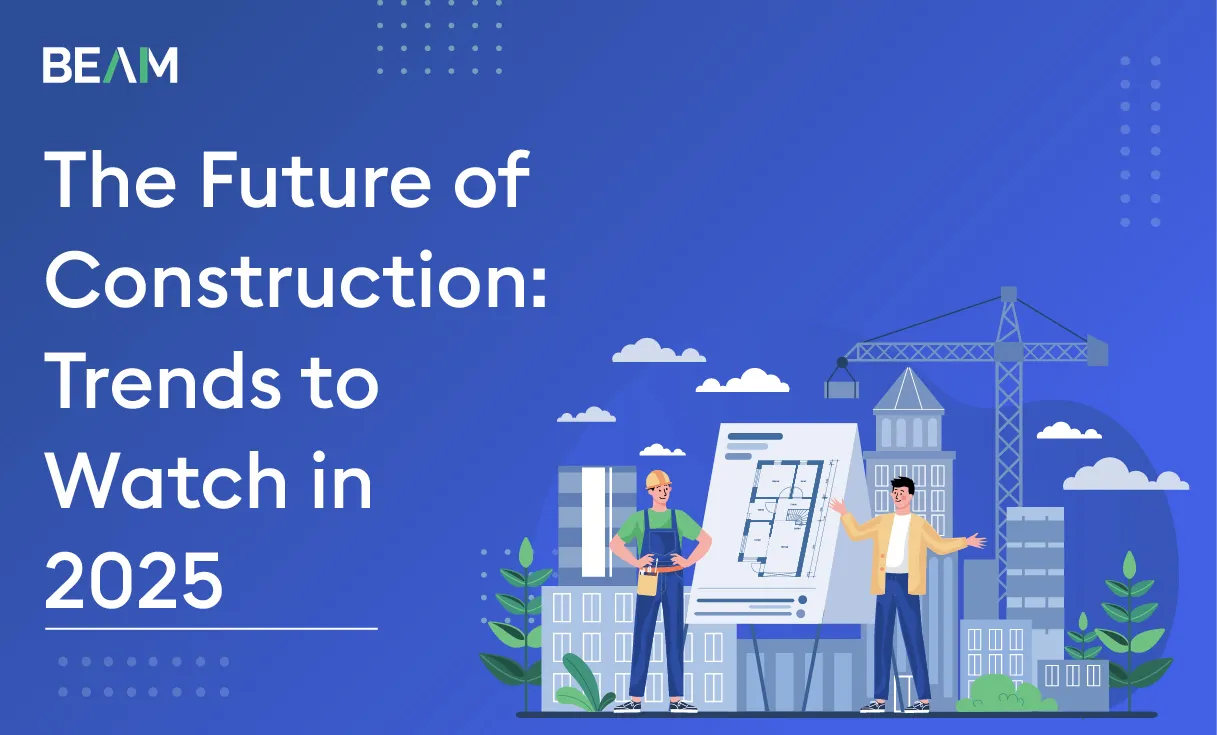
Imagine this: a construction firm in 2006 is thriving, riding the wave of a booming industry with 7.7 million workers at its disposal. Fast forward to 2024, and the construction industry has transformed dramatically: a record-breaking $2 trillion in spending, unprecedented growth, and over 8.3 million workers employed. Yet, challenges like: widespread labor shortages, rising costs, and an accelerating shift toward automation are rewriting the rules of success.
Staying ahead of these trends isn't just about keeping pace, it’s about future-proofing your business. In this article, we’ll look at the key trends and challenges shaping construction in 2025.
1. Building an agile workforce to manage labor shortages
The construction industry faces a significant talent shortage. Experts say that the industry must hire 501,000 additional workers to meet labor demand. Attracting workers is one of the biggest challenges construction firms face today, and it isn't just about numbers–it’s about attracting the right talent for increasingly specialized jobs.
Both skilled positions (like electricians and welders) and unskilled roles are becoming harder to fill. The problem is even worse on active construction sites, where securing enough labor to keep projects moving is a constant struggle.
The situation is complicated by the rise of high-tech construction projects, like data centers, semiconductor facilities, and other massive undertakings. These projects need workers with specialized skills, making competition for talent even fiercer.
For instance, building a large data center creates around 1,700 jobs in the local area over 18 to 24 months. However, this demand for workers often outpaces supply, leaving firms scrambling to hire and train talent.
Why this matters for 2025:
- Evolving Skillsets: By 2030, nearly half of today’s infrastructure skills will evolve within five years, requiring a balance of traditional, digital, and interpersonal skills.
- Aging Workforce: With the average age of craft workers approaching 46 by 2030, the urgency to attract younger talent has never been greater.
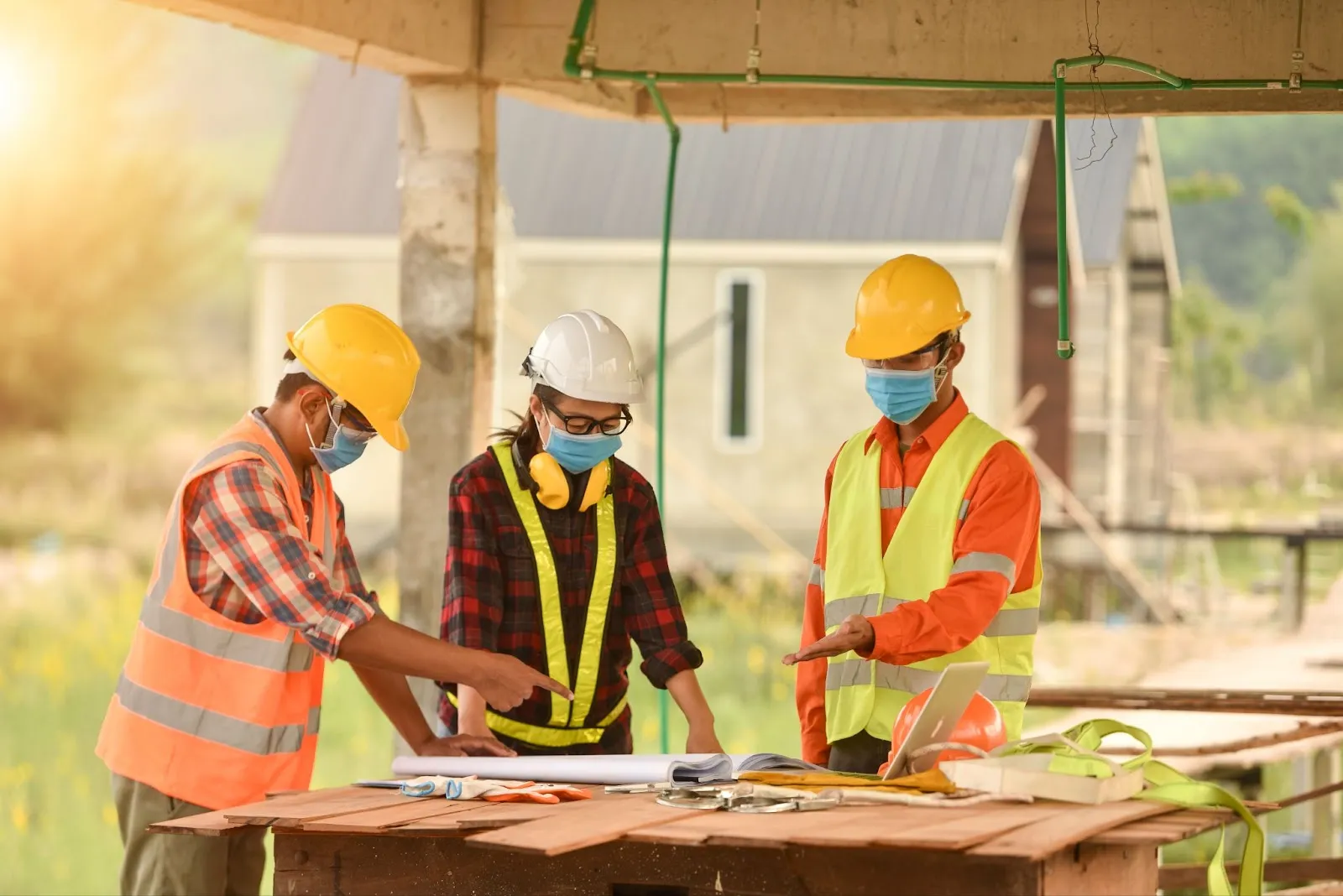
What can companies do to hedge against this?
Tap into AI-based solutions
AI-powered tools such as Beam.ai can help increase workforce productivity by freeing up time so that workers can focus on more strategic tasks. For instance, in the preconstruction phase, takeoffs are crucial for quantifying materials and creating accurate project estimates. However, it is often time-consuming. 50% of a typical bid cycle is consumed in doing takeoffs.
"AI tools like Beam AI automate this process. All you need to do is upload site plans and define scope of work. AI does the takeoffs for you. Results? Contractors and estimators can save time and focus on higher-value tasks."
Besides, AI-powered technologies like robots and autonomous machines can handle tough, physical tasks like drywall installation, allowing workers to focus on more specialized and important jobs.
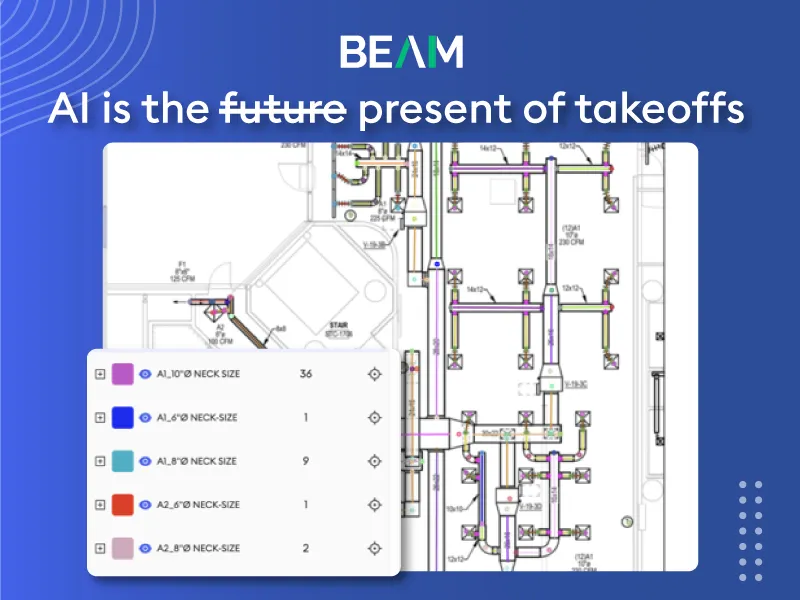
Offer clear growth paths
High turnover rates can be addressed by creating clear paths for career growth and skill development. Create opportunities for job rotation and cross-training. This keeps roles exciting and equips workers with diverse skill sets, thus increasing retention.
Embrace AR and VR for training
Use immersive technologies to upskill workers, preparing them for the evolving demands of high-tech projects. Training tradespeople and technicians to handle a variety of tasks not only builds diverse skill sets but also lets companies offer a more stable work environment, better pay, and engaging challenges.
2. Increased technology integration across the construction value chain
As construction projects grow in complexity, digital tools are no longer optional - they’re essential. Common advantages include increased process efficiency, accurate project planning and visualization, real-time collaboration, reduced risks, enhanced decision-making, cost optimization, and improved safety on-site.
Here are a few trends to look out for in technology in construction:
A. Building Information Modeling
Building Information Modeling (BIM) is a way to use technology to create a detailed digital version of a construction project. It brings together data from different sources to give everyone involved, like architects, engineers, and contractors, a clear and shared understanding of the project. By centralizing data, BIM improves decision-making and reduces delays.
B. Digital Twins
Digital twin technology is helping companies add more value by using digital replicas to simulate and optimize workflows, improving efficiency and addressing labor shortages. . For example, a U.S. based infrastructure consulting firm, Jacobs Engineering, is using digital twins and augmented reality to improve processes and address labor shortages.
C. Robotics and Automation
The construction industry still relies heavily on manual labor, with many tasks being repetitive and time-consuming. That’s where robotics and automation come in. These technologies speed up processes, minimize human errors, and reduce fatigue-related delays. For example, collaborative robots (or cobots) can handle tasks like bricklaying, welding, rebar tying, and painting with incredible precision.
On a larger scale, robotics can automate heavy equipment for jobs like excavation, transporting materials, lifting loads, pouring concrete, or even demolition. The benefits include faster project completion, improved safety for workers, and reduced labor needs—all while boosting overall productivity.
3. Green trends to watch out for in the construction industry
Sustainability and environmental responsibility have become central to most industries, driven not only by ethical considerations but also by legal mandates to cut carbon footprints.
In the construction sector, this translates into a commitment to green building practices, ranging from installing energy-efficient windows and doors to using fixtures and plumbing made from recycled materials, all aimed at crafting sustainable, eco-friendly structures. Let’s look at some of the green trends in construction in 2025:
Alternative Building Materials:
Materials like cross-laminated timber (CLT), 3D-printed concrete, and self-healing concrete are gaining traction for their sustainability and efficiency. Other cutting-edge options, such as mycelium composites and carbon nanomaterials, are becoming viable alternatives to traditional materials.
A. Green Buildings:
Green building is allowing firms to use resources wisely to create healthier and more eco-friendly structures. These buildings are cheaper to maintain and have a smaller impact on the environment. This approach considers every stage of a building’s life—from choosing the location and designing it to construction, use, upkeep, renovations, and even demolition.
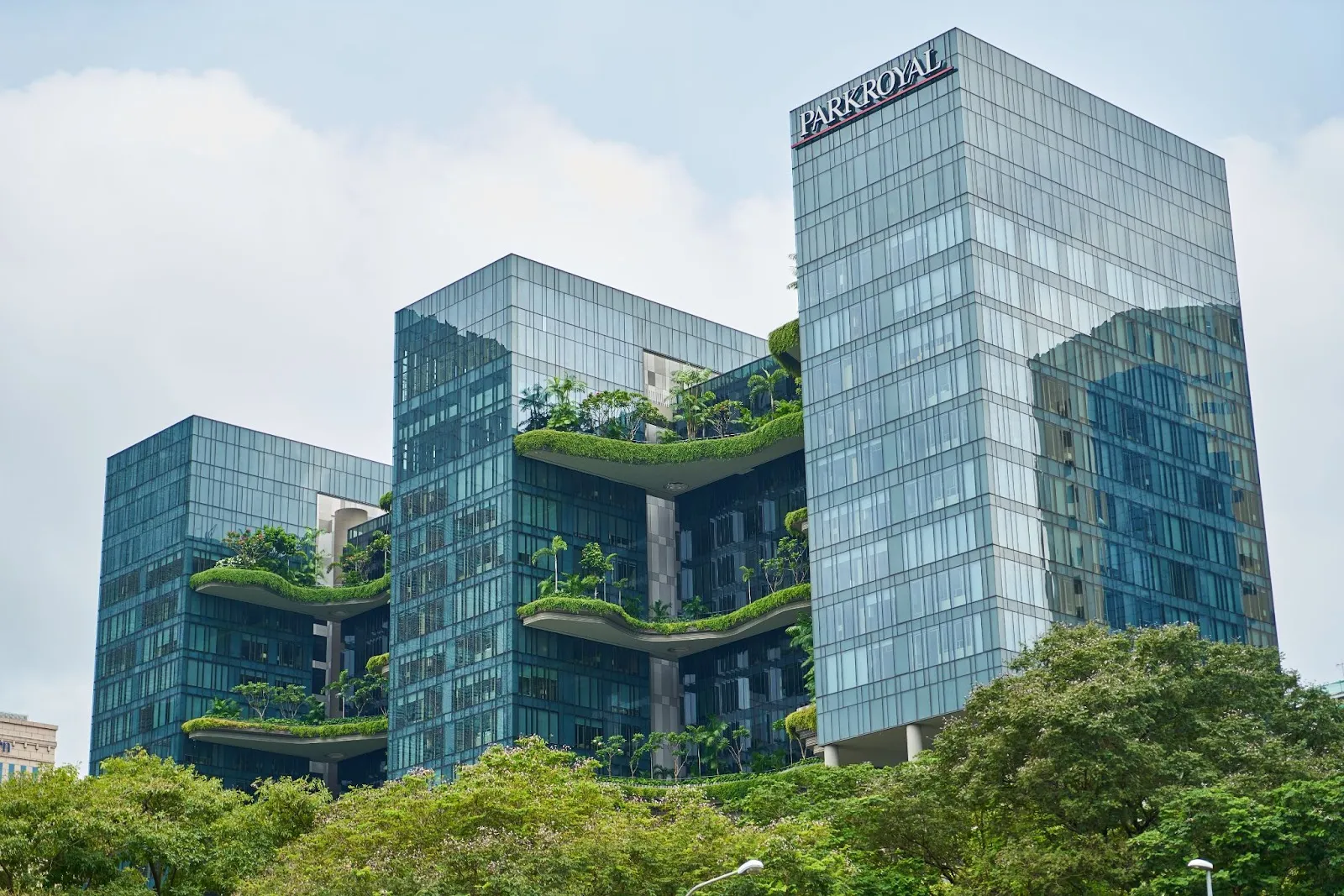
B. 3D printing
3D printing in construction, or additive construction, is a modern and eco-friendly building method. It uses construction printers to create entire buildings or specific parts layer by layer with advanced materials, often guided by digital models.
This process is highly flexible, reduces waste, needs less labor, and minimizes errors by being fully automated. Startups like ICON are already delivering 3D-printed homes in as little as 24 hours.
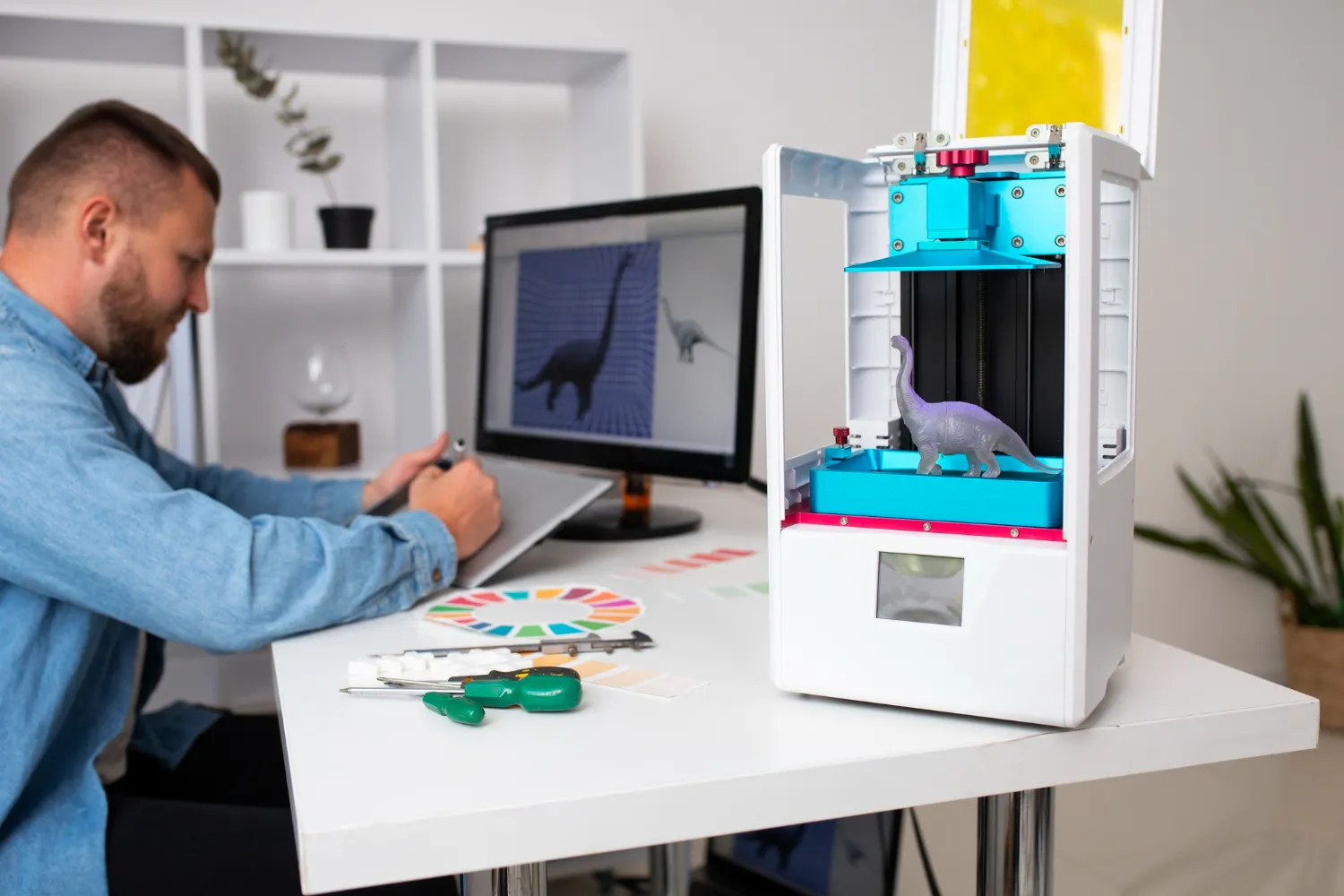
Over to you
To sum up, the construction industry in 2025 is navigating a seismic shift, driven by labor shortages, rising costs, and growing automation. Firms must address talent gaps by using AI tools, offering upskilling opportunities, and integrating technologies like robotics to enhance efficiency and reduce human error.
Digital advancements, such as Building Information Modeling (BIM), digital twins, and automation, are transforming project planning, collaboration, and execution. Sustainability remains at the forefront, with innovations like green buildings, 3D printing, and alternative materials leading the charge.
These trends are shaping a more efficient, eco-friendly, and future-ready construction industry.
Table of content
.webp)