Table of content
Ura is a skilled construction and real estate writer, with a focus on crafting content that bridges industry knowledge and storytelling.
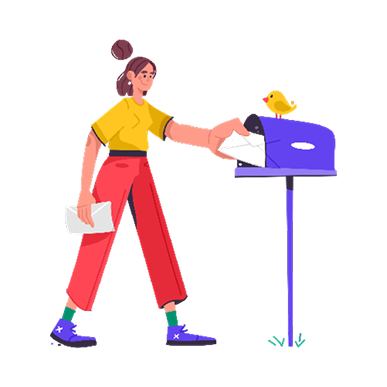
Top 6 Quantity Takeoff Mistakes to Avoid in 2025
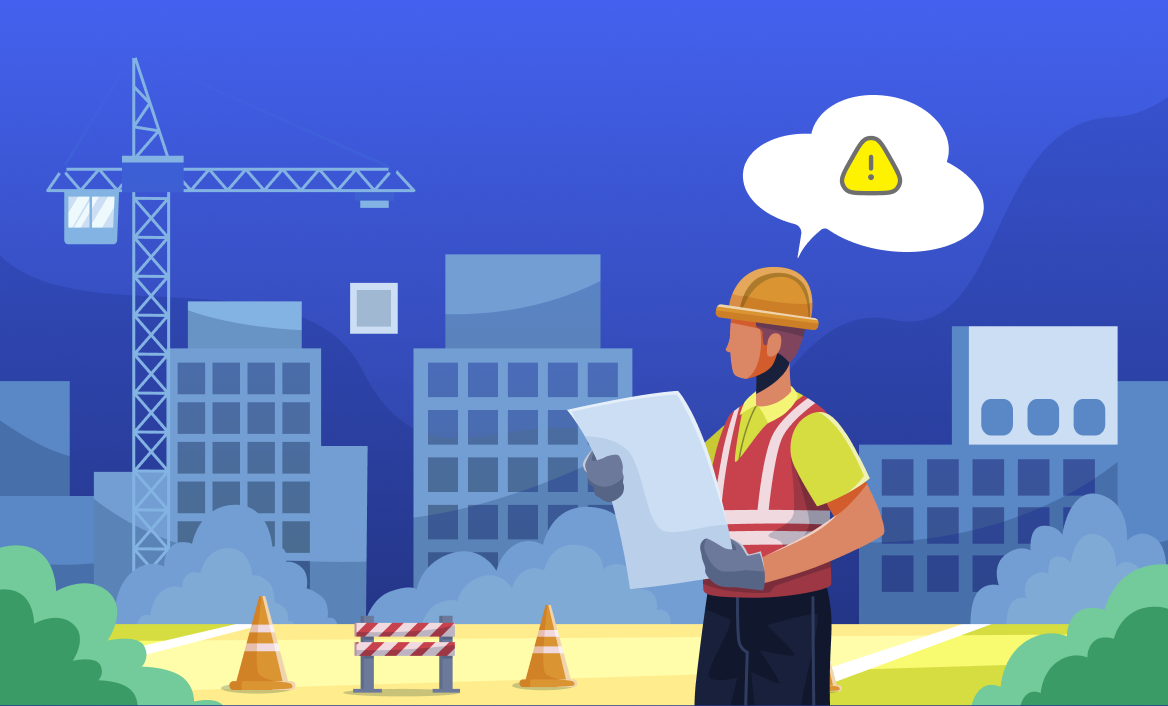
You’ve finalized your quantity takeoff for a new school build; this is one of your biggest projects yet. The design is complex, timelines are tight, and the itch to perfect everything is at its peak.
Then, right in the middle of construction, you notice an error. There’s a concrete shortage, and you have no idea where it all went wrong. After some digging, the issue is clear: The slab thickness was miscalculated in your quantity takeoff.
Suddenly, your dream project has turned into your worst nightmare. Deadlines are getting closer, costs are piling up, and your client is growing more frustrated by the day. Why? All because of a tiny oversight in the quantity takeoff that could have been avoided.
Accurate quantity takeoffs are the backbone of any construction project. But even minor slip-ups, such as missing a detail in a slab spec or misreading a plan revision, can lead to budget overruns, timeline delays, and unhappy clients.
Whether you’re a quantity surveyor, estimator, contractor, or project manager, understanding the most common quantity takeoff mistakes beforehand can save you a lot of stress down the road.
Let’s break down the top 6 quantity takeoff mistakes to avoid in 2025, helping you build more accurately and avoid last-minute surprises.
6 Quantity Takeoff Mistakes You Should Avoid
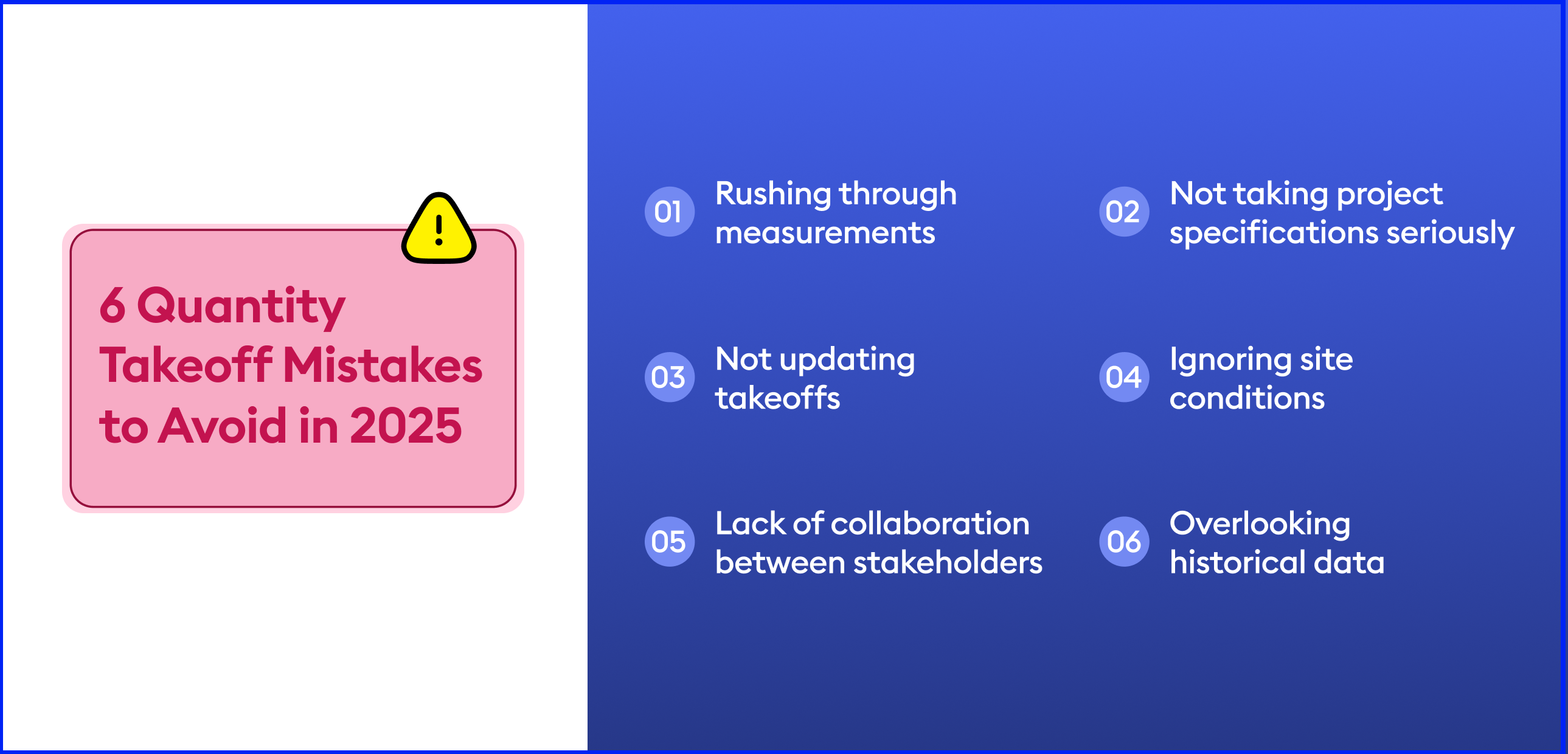
Mistake #1: Rushed Measurements = Compromised Project
Incorrect dimensions or area calculations can majorly impact material quantities and overall costs. For instance, misreading floor dimensions during takeoff will lead to material shortages and project delays. With increased labor hours because of expensive rework, you'll find yourself scrambling to meet already tight deadlines and dealing with frustrated clients.
With manual quantity takeoffs, the process becomes even more challenging. When you have estimators flipping through hundreds of plan sheets by hand, all while trying to meet unrealistic deadlines, mistakes can happen—and those mistakes can get expensive, fast.
Fortunately, AI is now solving this very manual quantity takeoff problem. Tools like Beam AI automate the entire takeoff process, eliminating the need for manual effort. By handling the heavy lifting, Beam AI can save up to 90% of your time. That frees you up to focus on the strategic aspects of your job, such as coordinating with vendors, refining your bids, and winning more projects.
Want to know how Beam AI can automate your takeoffs? Talk to us!
Mistake #2: Not taking project specifications seriously
In the rush to meet deadlines or juggle multiple bids, it’s easy to skim past details in the project specifications, especially when the drawings seem straightforward at first glance or you’ve worked on similar jobs before. But specs often contain specific product requirements, installation methods, and performance criteria that can significantly impact your quantities and pricing.
For example, if you price a plumbing system using standard PVC pipes but the spec sheet actually calls for copper, it can result in costly reworks and damage your client’s trust.
The fix? Make specification reviews a non-negotiable part of your takeoff process. Use checklists, flag any unusual requirements, and ensure that every team member has access to the latest version of all documentation.
When your team has easy access to the latest specs and drawings, they can stay aligned and catch potential discrepancies before they become unnecessary overheads.
Mistake #3: Not updating takeoffs
Creating the initial takeoff is already a big task. But keeping it updated as things evolve? That’s a whole different challenge, especially when estimators are doing it manually.
Last-minute spec changes, a client request, design modifications, or unexpected site conditions; if your takeoff doesn’t reflect recent updates, your project can go off track.
Automated takeoff software like Beam AI can help here. All you need to do is upload the addenda, and the software automatically picks up new quantities. This also enables you to save time on comparing plans and flagging new quantities. Plus, with everything in one place, your team of vendors can access the latest specs and stay aligned.
Mistake #4: Ignoring site conditions
Designs and drawings might look perfect on paper, but execution often tells a very different story.
Let’s say you’re estimating materials for a small retail building. The plans show a simple layout, and you assume the site is flat. But when the team arrives, they discover uneven land with a noticeable slope. Suddenly, your original plan no longer works. You now need extra fill, adjustments to the design, and maybe even retaining walls. These changes don’t just impact design; they drive up concrete and labor costs, delay permitting, and can throw your schedule off by weeks.
This is why you can’t ignore site conditions. And it’s not just about the construction logistics —it’s also about your team’s safety. Unexpected factors like poor soil conditions or bad weather can quickly drive up labor costs, delay project timelines, and create serious safety risks on-site.
Avoid this by conducting thorough site assessments beforehand. Review soil reports, terrain conditions, and even drainage details to ensure your estimates align with real-world site conditions.
Mistake #5: Lack of collaboration
Even with drawings, specs, and addenda in place, construction projects move fast, and collaboration gaps still happen.
Take this, for example: your estimator completes the takeoff for a multi-unit residential project based on the issued drawings. A few days later, the structural engineer shares a clarification about beam sizing that slightly changes the framing layout. The update is captured in an addendum, but it gets buried in email or isn’t synced across the entire project team.
The result? The bid goes out based on outdated assumptions. And while the mistake is caught later during procurement, it leads to last-minute changes, rework, and unnecessary stress that could’ve been avoided with tighter coordination.
That’s why regular check-ins, shared folders for drawing updates, and using takeoff software with sharing capabilities can go a long way. The goal should be to make sure everyone sees the same version of the truth.
Mistake #6: Overlooking historical data
Your past projects are a gold mine of lessons if you take the time to dig into them.
Before starting any new quantity takeoff, it's worth going back and reviewing similar jobs you've done in the past. Why? Because patterns often repeat themselves. Certain materials always run short, or specific trades consistently blow past the budget. If you take the time to look, you’ll usually find warning signs.
For example, you’re estimating for a new hospital project. At first glance, everything looks fine, but then you pull up data from a couple of similar hospital builds you worked on before. Plumbing costs almost always ran about 10% higher than your initial estimates.
Now, because you caught it early, you can plan for it. Build in a buffer. Flag it as a potential risk. Have that conversation with the team upfront.
Before You Go: A Final Look at Quantity Takeoff Mistakes
Quantity takeoffs might feel like just one part of the bigger pre-construction picture, but they’re actually far more critical. After all, this is where you determine everything that will eventually make up the build. Hence, accuracy is non-negotiable, and everything hinges on getting it right.
As we’ve seen, even the most minor errors can lead to significant losses and strain client trust. The good news? These issues are entirely avoidable with the right systems, solid collaboration, and the right tools in place.
At the end of the day, it's not just about counting materials; it's about setting the foundation for a successful, stress-free project. So slow down when it counts, double-check the details, and stay connected with your team. Because when your takeoff is on point, everything else has a much better chance of falling perfectly into place.
And if you’re looking for the right takeoff software, Beam AI is the ONLY AI-based automated takeoff software that does takeoffs for you. Yes, you upload site plans, define the scope of work, and AI takes off quantities for you. An experienced estimator then validates the takeoff before it's sent to you within 1-3 days.
Want to know how Beam AI can boost your bidding capacity? Book a demo today.